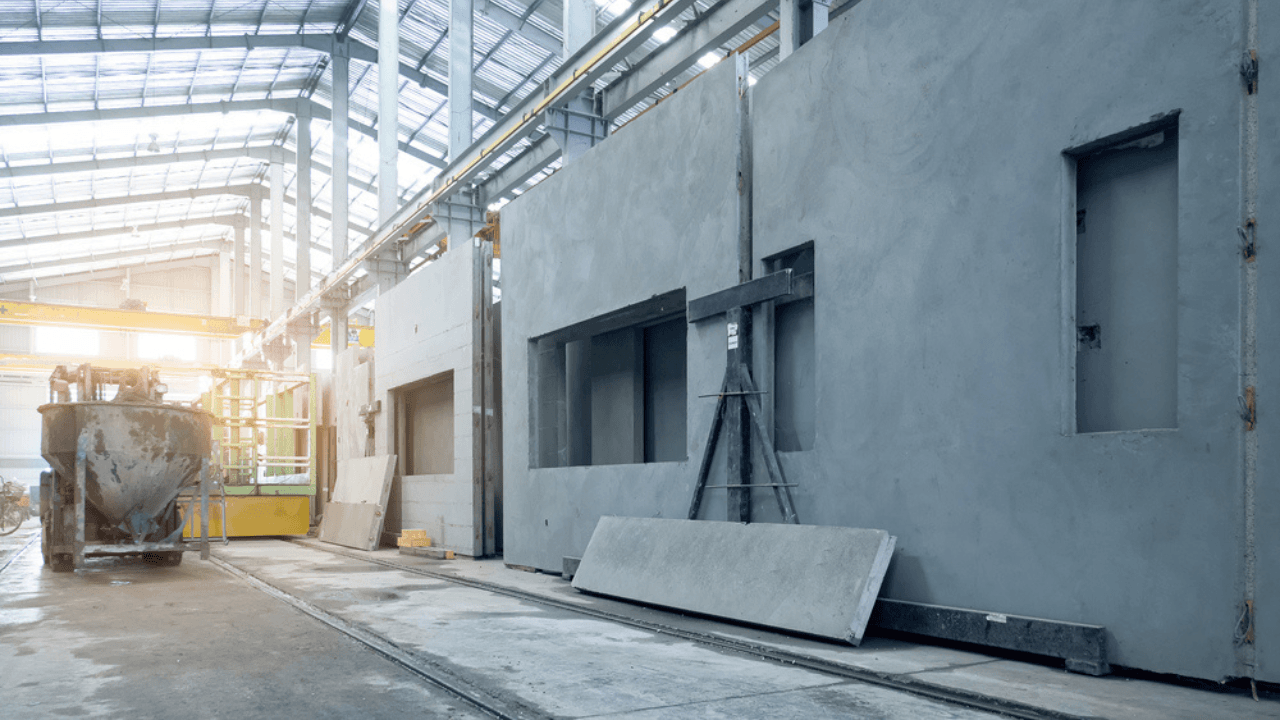
Leveraging on Contactless Technology to Track and Locate Prefabricated Components
By Lu Chang Peh1, Shijing Lin2, Ziwen Liu3, Kelvin Tan4
SYNOPSIS:
With strong promotion from numerous governments, prefabricated building components (PC) have been widely embraced by the built environment industry while leveraging on its benefits of enhanced project management, shorter project duration, better control of labour and quality assurance and so on. However, the existing method of tracking PC is still widely implemented using paper-based methods, which is laborious and error-prone, making it difficult to maintain and track PC over time. Using traditional methods to identify, track, and locate PC can potentially lead to a range of operational issues such as component mishandling and misplacement, as well as wrong installation. To remedy these deficiencies, this study proposes an automated method for achieving PC traceability based on a digital platform and contactless technologies. The prototype consists of four key parts: PC directory, wall chart, dashboard and records. The PC directory is a configuration file for all components and tracks the status of all PC components in one centralised location; the wall chart enables the visualisation of the progress of production, delivery, and installation in real time; the dashboard tracks the progress of the entire project at a glance; the records allow updating of digital components’ records via QR code on-the-go. Through this prototype, we can digitise and visualise the entire value chain of PC production, delivering to installation with greater transparency and efficiency. This approach has been validated in some public housing projects, and the results have indicated an improvement in operational cost and productivity.
Keywords: Automated tracking and locating, contactless technology, integrated digital delivery (IDD), prefabricated components, just-in-time (JIT) delivery.
1 Associate Professor and Vice Dean, School of Science and Technology, Singapore University of Social Sciences, 463 Clementi Road, Singapore 599494
2 Co-Founder and CEO, Hubble Pte. Ltd. 2 MacTaggart Rd, #08-01, Singapore 368078
3 Faculty, School of Science and Technology, Singapore University of Social Sciences, 463 Clementi Road, Singapore 599494 (*corresponding author). Email: zwliu001@suss.edu.sg
4 Senior Marketing Manager, Hubble Pte. Ltd. 2 MacTaggart Rd, #08-01, Singapore 368078
1. Introduction
Traditionally a laggard in terms of technological advances and adoption due to inherent characteristics such as the onsite nature of projects and skilled labour shortages, the construction industry is increasingly looking to other industries such as aerospace and information technology, to learn and apply what emerging technologies work for them to work for us. In Singapore, one of the catalysts was Integrated Digital Delivery (IDD) which triggered the implementation of various technologies. Building and Construction Authority (BCA) [1] introduced IDD in October 2017 as an entire lifecycle project delivery approach, which utilises digital technologies to digitally integrate the work processes and stakeholders along the value chain. In the supply chain for construction sectors, problems with improperly classifying, tracking, and locating highly customised prefabricated parts lead to delayed deliveries, double handling, lost, and incorrect installations, which cause schedule delays and higher labour costs [2,3]. Hence, the objective of this study is to propose a novel cloud-based digital fabrication management platform which would be able to use contactless technologies to generate an asset register to schedule and track prefabricated components from fabrication, to delivery, to assembly and installation on site.
The structure of the paper is organised as follows: Section 1 is the introduction; Section 2 is a literature review on the underpinning technologies and comparable solutions; Section 3 elaborates on the digital platform in terms of how it works; Section 4 is the validation of the platform/system through a real public project; and finally, Section 5 is the conclusion where findings and recommendations are discussed.
2. Literature Review
2.1 IDD, DfMA and IDD enables DfMA process
According to BCA [1] that “Integrated Digital Delivery (IDD) is the use of digital technologies to integrate work processes and connect stakeholders working on the same project throughout the construction and building life-cycle. This includes design, fabrication and assembly on-site, as well as the operations and maintenance of buildings.” With the implementation of IDD in the construction sector, IDD research has attracted the attention of a number of scholars. For instance, Hwang et al. [4]’s study evaluated the level of IDD implementation and the perceived benefits in project performance, and identified 32 digital and cloud technologies across the four phases of IDD. In addition, they also found that only 38.71% of the local industry employed IDD technology throughout all four IDD phases. Liu et al. [5] used a combination of scientometric analysis and IDD thematic discussion to investigate 471 scholarly bibliographies Exchange from the Web of Science (WoS) database, reiterating 10 digital use cases of BIM-sustainability in the IDD lifecycle and highlighting obstacles and areas for further research. Recently, a survey questionnaire was used to identify and analyse 25 hurdles to IDD implementation and 18 strategies to overcome the barriers and enhance IDD implementation based on the literature study [6].
2.2 Tracking-related efforts and enabling technologies
The infusion of emerging technologies into construction management has improved costs, schedule, quality and safety [7]. Bell and McCullouch’s research has supported the use of barcodes in areas such as quantity take-off, field material control, warehouse inventory and maintenance, tool and consumable material issue, timekeeping and cost engineering, purchasing and accounting, and document control and office operations [8].
Researchers and construction companies have continually explored and studied various ways to further enhance construction operations and management. For instance, Lee et al. conducted a survey and found that there was an opportunity for implementing QR codes in conjunction with mobile IT [9]. They also found statistical evidence that using QR codes can lead to significant time savings. Harper et al. explored the use of instrumentations and sensor technologies, such as remote sensing, real-time kinematics, GPS, digital handheld devices and radar for highway design and construction projects [7]. Abbott and Chua studied and developed a framework to merge RFID and BIM to optimise construction, delivery and installation of PPVC units in construction [10].
The QR code differs from a bar code in terms of its physical dimensions: it is a 2D matrix code which provides high data storage capacity, fast scanning, omnidirectional readability and error correction [11]. On the other hand, compared to radio-frequency identification (RFID), it is more accessible and affordable, making it more attractive for small businesses and construction projects. Due to these advantages and benefits, it’s acceptance across industries and worldwide has grown rapidly over the years with the advancement and proliferation of smartphones and tablets [9]. Notably, there are static QR codes and dynamic QR codes. There are a number of advantages a dynamic QR code has over a static one, such as: it can be edited, takes less time to scan, and most importantly, offers QR scan tracking and analytics [9,11]. Compared to a bar code or static QR code, dynamic QR codes can hold much more information. In addition, they are more economical than RFID, and they can be integrated with the digital fabrication management platform for the tracking and location of prefabricated components. It is staunchly believed, and later proven in our study that this can reap benefits such as optimisation of construction logistics, minimisation of damages during installation and reducing reworks eventually, performance of construction project analytics et al, leading to desirable project outcomes such as keeping to project schedule, improved construction quality and significant time savings.
3. Research Gaps
During the onset of the COVID-19 pandemic, construction projects in Singapore using prefabricated modules were facing delays of up to nine months. This affected over 11,000 residential housing units’ construction. Despite the Prefabricated Prefinished Volumetric Construction (PPVC) technique is often touted to cut time up and manpower, it has made things worse during the pandemic for the local contractors. With a lack of production sites, Singapore mainly gets PPVC supplies from foreign countries typically from Malaysia. However, the implementation of Malaysia Government Movement Control Order (MCO) has disrupted the entire supply chain with minimum supply of PPVC modules. This has made it complex to track its delivery let alone identifying of resources and equipment ahead of time onsite. Even if the PPVC modules can be delivered in advance, there’s nowhere to store them due to a lack of holding facilities. The limited facilities available in Singapore for storing these PPVC modules have also resulted in increased operating costs which would evidently erode the advantage of off-site construction.
4. Proposed IDD Platform
In addressing the above-mentioned issues and ensure just-in-time (JIT) delivery to avoid shortage of materials onsite, a digital tracking platform was proposed in this study. The proposed digital tracking platform incorporates a dynamic and distributed solution using dynamic QR codes technology for automating the identification and tracking of individual precast components to the more complex and integrated PPVC modules. The tracking processes for precast components and PPVC modules can be divided into 3 main phases including: off-site production phase, delivery phase and onsite installation phase.
In the off-site production phase, precast components are fabricated. Further steps in the off-site process include quality control, handling, and storage, and picking up and loading of these precast components. These precast components would then be assembled to form the PPVC modules either during the off-site production phase prior to shipping out or upon being delivered to the actual onsite installation site. The final onsite installation phase involves the receiving of the precast components and PPVC modules at the construction site. The processes governing most residential housing building projects are similar in context, involving a high mix of individual precast components and PPVC modules to be tracked as shown in Figure.1.
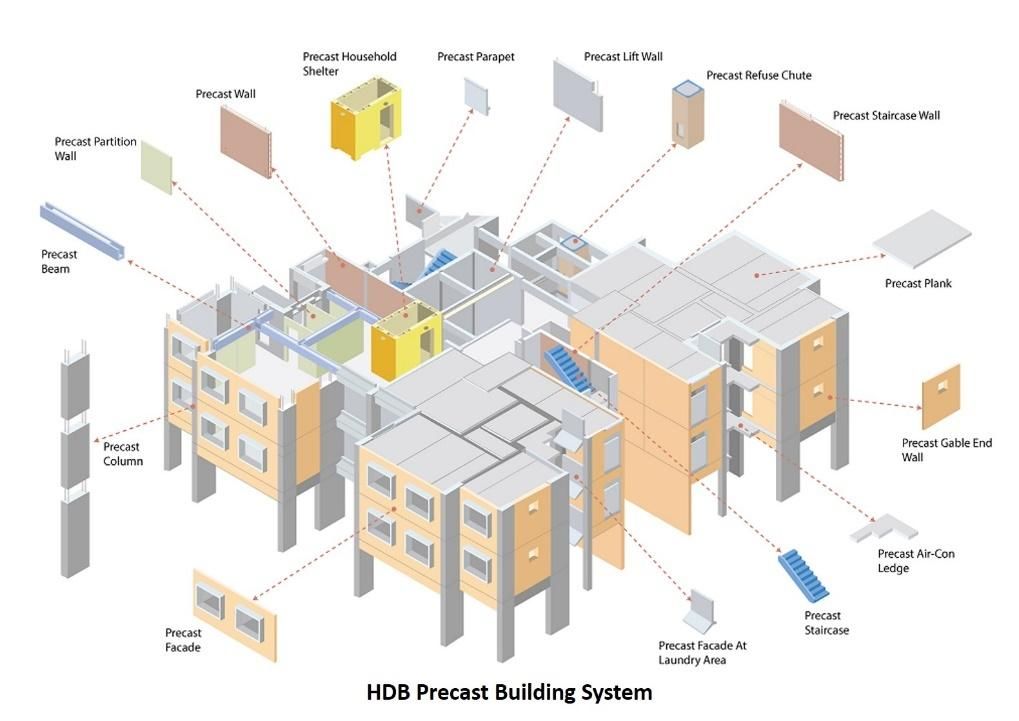
Figure 1. Precast building system [12]
Figure 2 depicts a schematic model of data collection during off-site production, delivery and onsite installation. In this approach, data collection and installation position determination begin when an order for prefabricated components / PPVC modules is placed.
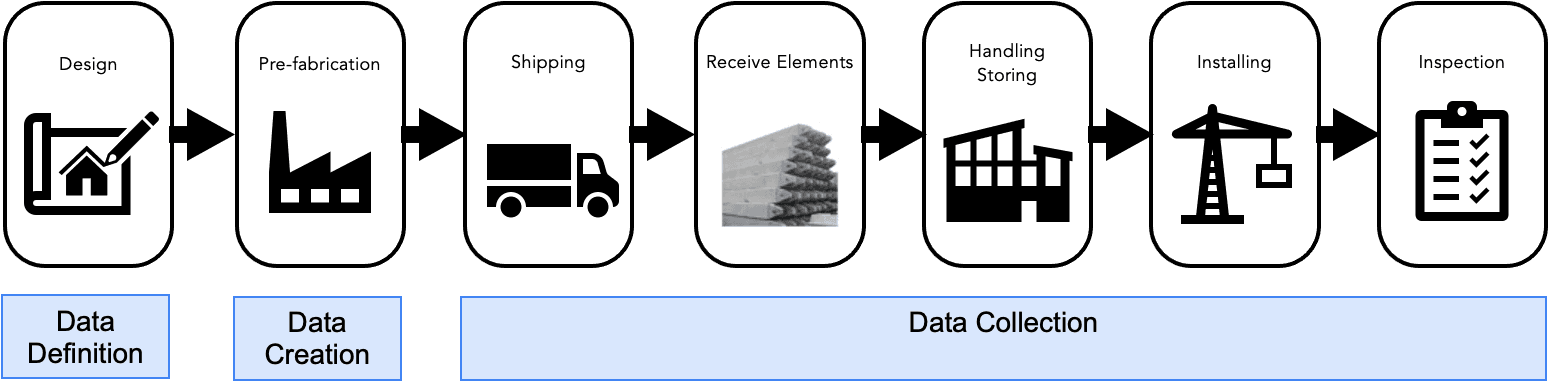
Figure 2. Data collection during production, delivery and onsite installation
Following that, the fabrication component information and installation position would be described in the data structure of the IDD platform. It is recommended that the following types of information be stored in the data structure:
- Identification information such as component type name, ID code and so on.
- Task-specific information such as component installation location, etc.
- Planning information such as target production dates, delivery dates, installation dates and so on.
- Status information, such as status (not started, in production, ready for delivery, on delivery, delivered, delivery inspected, installed and installation inspected)
After that, the data structure would be utilised to store, share, manage, and integrate collected data with tools and workflows under the proposed platform.
When the prefabricated component is manufactured, or ready for delivery, it will be tagged with the dynamic QR code label generated by the proposed platform. Another alternative for tagging prefabricated components is to do it onsite during the installation phase, as illustrated in Figure 3. Upon arrival of the prefabricated components, the printed QR code will be manually attached to the prefabricated components.

Figure 3. Material management activity timeline with QR code
On-site personnel could then scan the QR code label with the mobile app on their mobile devices to update its status on-the-go. The proposed platform processes the updates and sends them to the Wall Chart model, which incorporates colour coding according to component status and aggregates the data into standard units.
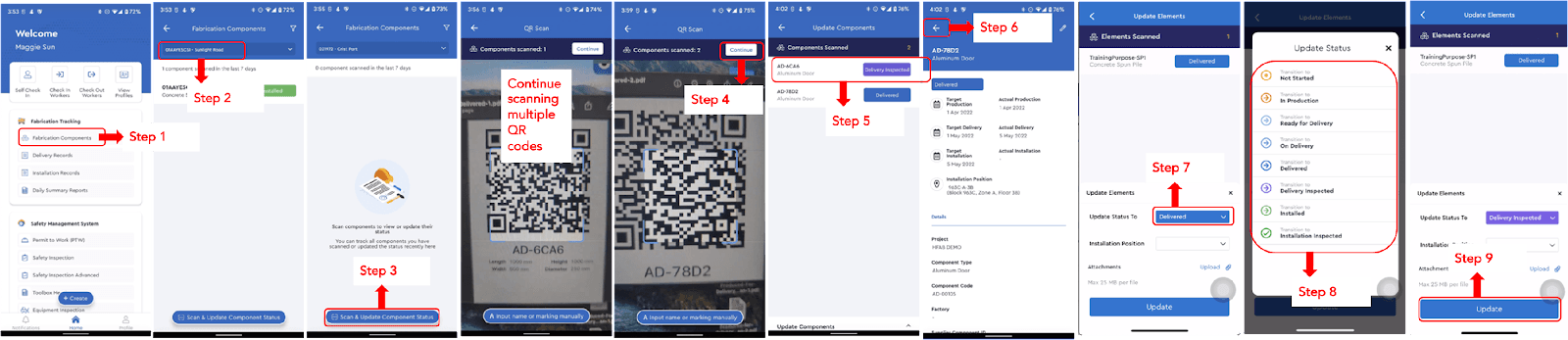
Figure 4. Upload precast components status via mobile device
As illustrated in Figure 5, the colour will change in the order of grey, blue, purple, and green depending on the assigned status of not started, produced, delivered, and installed. This allows for a quick and simple approach to visualise progress by converting it into a digital depiction that resembles the elevation and plan that are usually displayed in Excel.
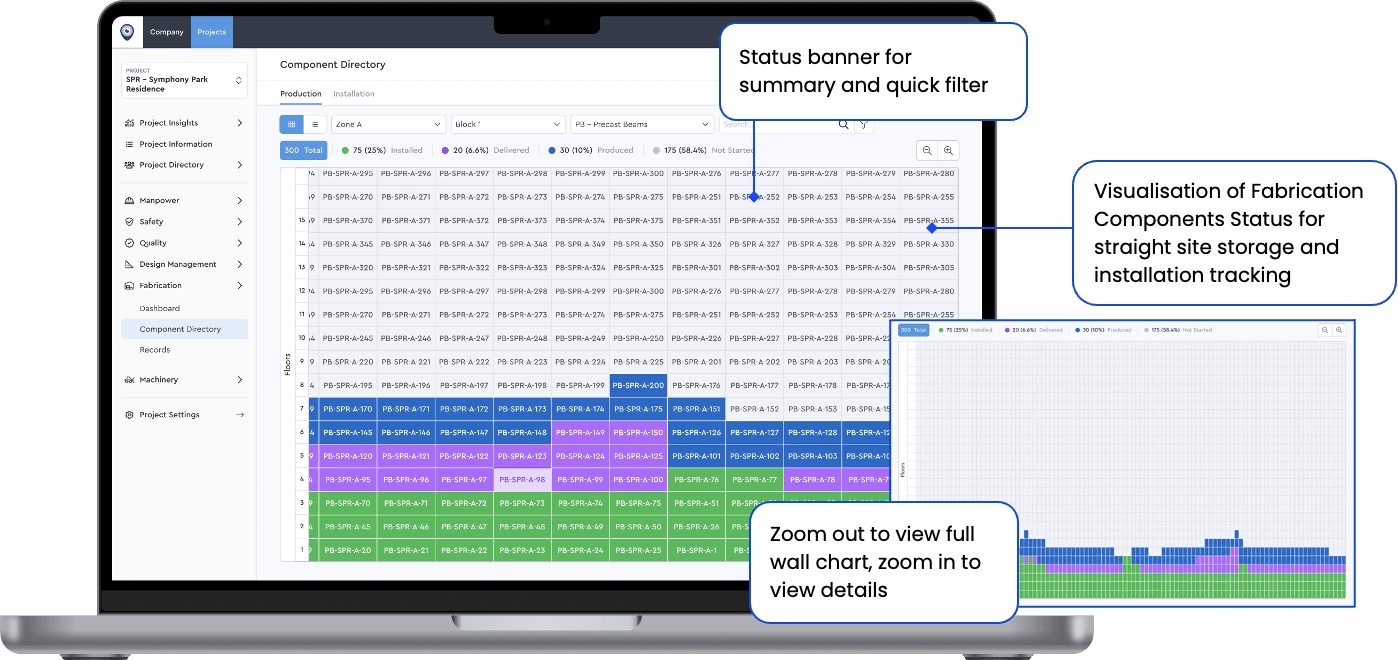
Figure 5. Wall chart model
The proposed IDD platform integrates with Building information modeling (BIM). By interfacing to the BIM, the status information can also be presented graphically, with each component coloured according to its status such as pending, in production, inspected, in delivery, delivered and installed, which as illustrated in Figure 6.
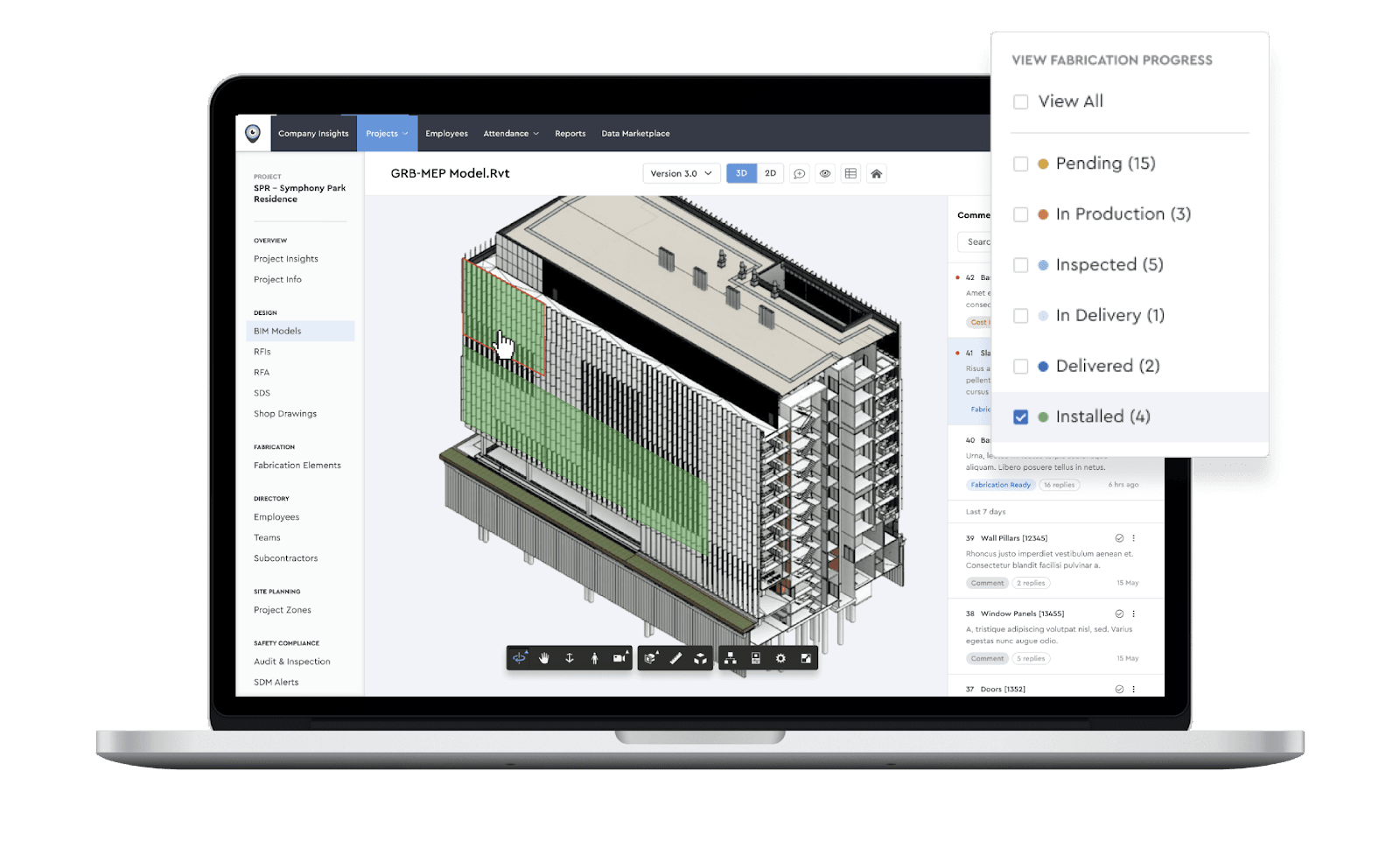
Figure 6. Status information displayed through BIM representation
In addition to tracking PCs, the proposed IDD platform is also capable of producing records for delivery, installation, and inspection as shown in Figure 7.
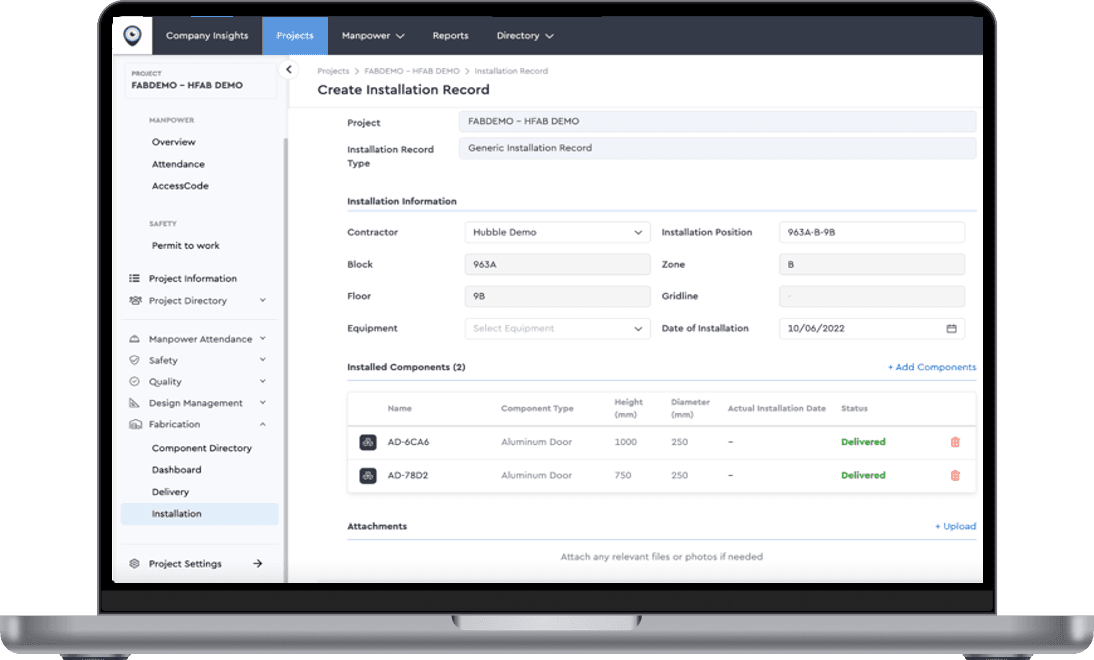
Figure 7. Example of an installation record created in the platform
Figure 8 illustrates how all component information is dynamically updated and displayed live. Having access to this collective information on an integrated platform allows stakeholders in the construction chain to exchange information and communicate wirelessly in real time, from precast suppliers in the upstream chain to contractors in the downstream chain, thereby assisting project managers in controlling and monitoring the construction process on site.
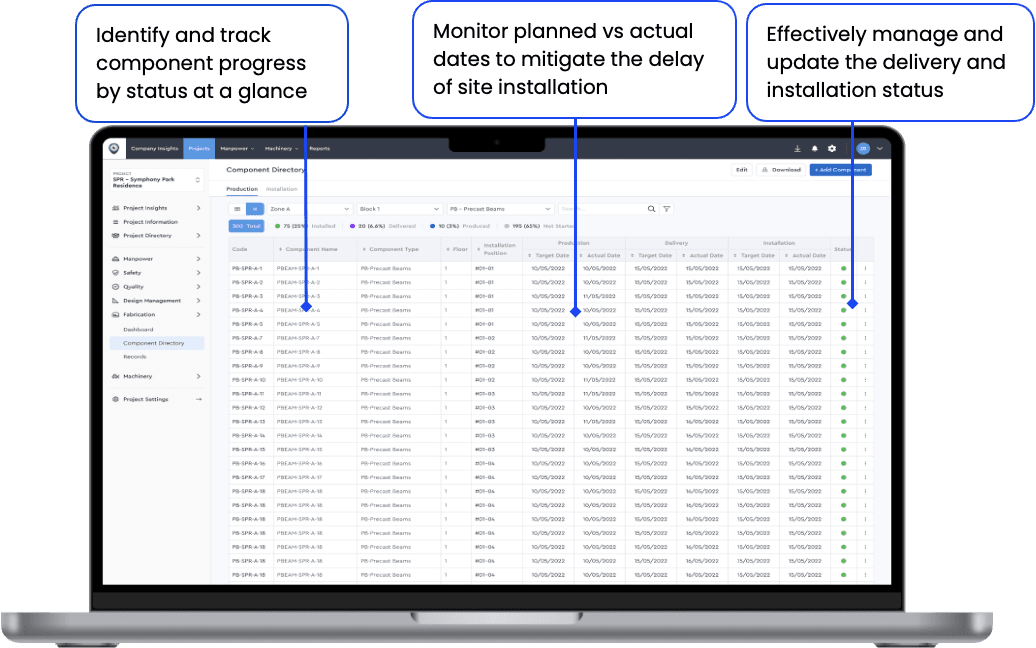
Figure 8. Illustration of the live component directory viewing list
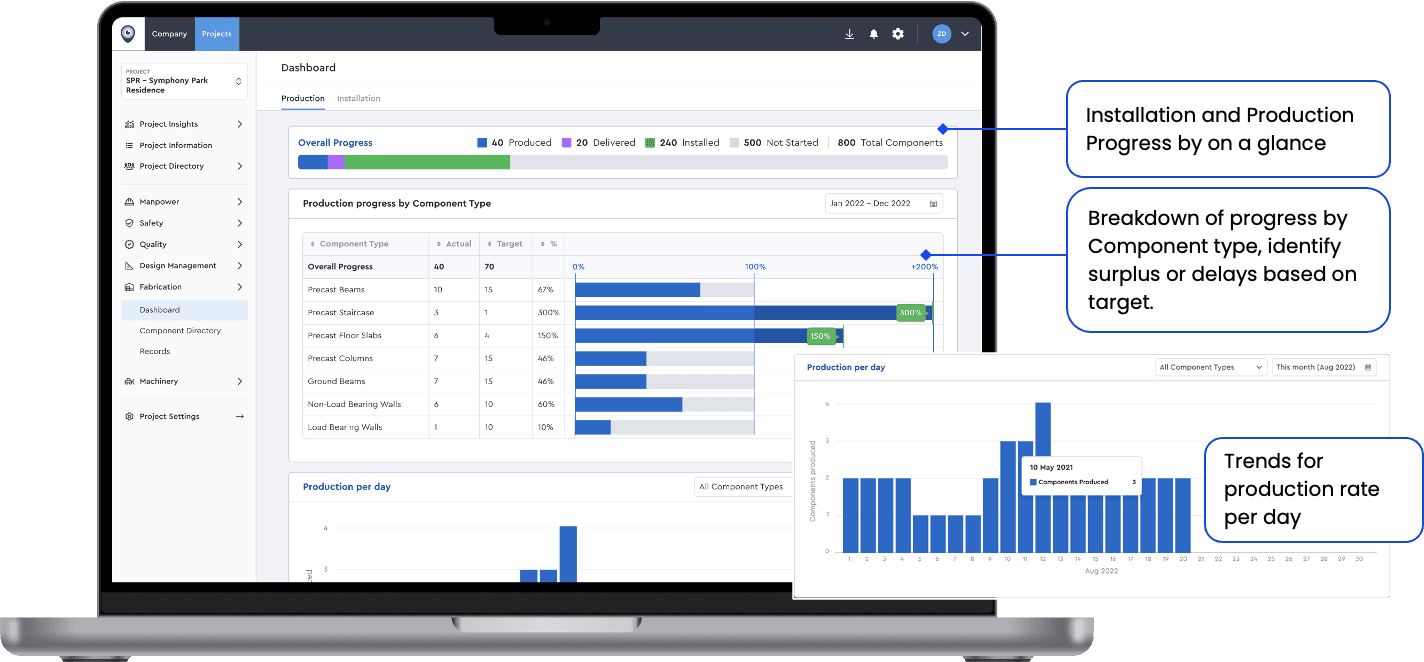
Figure 9. An overview breakdown of the overall progress in dashboard
Figure 9 shows how project stakeholders would operate in the new IDD environment in an integrated manner, sharing timely relevant information with the help of a project collaboration platform and common standards. Using all the data captured by the proposed platform, performance metrics can easily be assessed and displayed on the dashboard. Over time, the information collected from project to project will allow learning and further innovation to take place.
5. Validation and Conclusions
Performing a cost-benefit analysis of manual vs. QR code technology is necessary to validate the value of the proposed platform for construction management automation. It is challenging to estimate the actual process time and labour needed for certain tasks in construction management. However, it is possible to compare the fixed and variable costs with the potential benefits of the proposed IDD platform. Costing can be broken down into two categories: investment costs and operation costs. The fixed investment cost refers to the hardware used throughout the three main tracking phases from off-site production to onsite installation. In light of the fact that QR codes can be captured by any camera mobile device, and given that everyone has a camera mobile phone, it is not necessary to purchase any hardware apart from a printer to print the QR code labels. It is therefore reasonable and affordable for firms to adopt the fixed cost. As for the variable operation costs, they include sticker paper labels and GPRS network connectivity, as well as scanning labour costs. As the scanning of application forms can be integrated and manned into existing receiving processes, there is no need to recruit an additional headcount for the process. Thus, the variable cost largely relates to the costs associated with paper and network subscriptions. The benefit of utilising the Hubble platform can be experienced in many aspects of project management. These benefits can be direct, such as:
- Reduction of man hours spent hunting for components, assessing inventory conditions, and reducing surplus and waste components
- Reduce logistic complexity and avoid incurring expensive storage fees due to overestimating or overordering
- Reduced material management costs by guaranteeing availability of the right components at the right time, in the right quantity, and at the right place
In addition to the direct benefits, indirect and intangible gains are largely related to improving labour productivity and process efficiency with gains of up to 50%. Due to automation of labour-intensive tasks in material management, such as paperwork for recording, updating, and reporting the material status through daily check-ins and check-ups, costs for material management have reduced up to 20%. As an important point to note, the proposed IDD digital platform is able to track not only prefabricated components but also workers and equipment statuses across multiple locations without requiring additional fixed infrastructure.
In a nutshell, this study proposes an automated method for achieving PC traceability based on a digital platform and contactless technologies. The prototype consists of four key parts: PC directory, wall chart, dashboard and records. The PC directory is a configuration file for all components and tracks the status of all PC components in one centralised location; the wall chart enables the visualisation of the progress of production, delivery, and installation in real time; the dashboard tracks the progress of the entire project at a glance; the records allow updating of digital components’ records via QR code on-the-go. Through this prototype, we can digitise and visualise the entire value chain of PC production, delivery to installation with greater transparency and efficiency. This approach has been validated in some public housing projects, and the results have indicated an improvement in operational cost and productivity.
6. References
[1] Building and Construction Authority, Integrated Digital Delivery (IDD), (2022). https://www1.bca.gov.sg/buildsg/digitalisation/integrated-digital-delivery-idd (accessed October 25, 2022).
[2] J. Song, C.T. Haas, C. Caldas, E. Ergen, B. Akinci, Automating the task of tracking the delivery and receipt of fabricated pipe spools in industrial projects, Autom. Constr. 15 (2006) 166–177. https://doi.org/10.1016/j.autcon.2005.03.001.
[3] E. Ergen, B. Akinci, R. Sacks, Tracking and locating components in a precast storage yard utilising radio frequency identification technology and GPS, Autom. Constr. 16 (2007) 354–367. https://doi.org/10.1016/j.autcon.2006.07.004.
[4] B.G. Hwang, J. Ngo, P.W.Y. Her, Integrated Digital Delivery: Implementation status and project performance in the Singapore construction industry, J. Clean. Prod. 262 (2020) 121396. https://doi.org/10.1016/j.jclepro.2020.121396.
[5] Z. Liu, Y. Lu, M. Shen, L.C. Peh, Transition from building information modeling (BIM) to integrated digital delivery (IDD) in sustainable building management: A knowledge discovery approach based review, J. Clean. Prod. 291 (2021) 125223. https://doi.org/10.1016/j.jclepro.2020.125223.
[6] Jasmine Ngo; Bon-Gang Hwang; Priscilla Wan Yi Her, Construction Research Congress 2020 809, Constr. Res. Congr. 007 (2020) 809–818.
[7] C.H.D.T. and E. Jaselskis, Emerging Technologies for Construction Delivery, 2019. https://doi.org/10.17226/25540.
[8] L.C. Bell, B.G. McCullouch, Bar Code Applications in Construction, J. Constr. Eng. Manag. 114 (1988) 263–278. https://doi.org/10.1061/(asce)0733-9364(1988)114:2(263).
[9] H.W. Lee, B.A. Harapanahalli, C. Nnaji, J. Kim, J. Gambatese, Feasibility of using QR codes in highway construction document management, Transp. Res. Rec. 2672 (2018) 114–123. https://doi.org/10.1177/0361198118776133.
[10] E. Abbott, D. Chua, The Intelligent use of RFID in Prefabricated , Construction Work Flow and BIM Volumetric, MATEC Web Conf. 312 (2020).
[11] S. Tiwari, An introduction to QR code technology, Proc. – 2016 15th Int. Conf. Inf. Technol. ICIT 2016. 1 (2017) 39–44. https://doi.org/10.1109/ICIT.2016.38.
[12] Housing & Development Board, Prefabrication Technology, (2022). https://www.hdb.gov.sg/about-us/research-and-innovation/construction-productivity/prefabrication-technology (accessed October 25, 2022).
Share this article
Explore Related Content
Stay up to date with our latest news features!
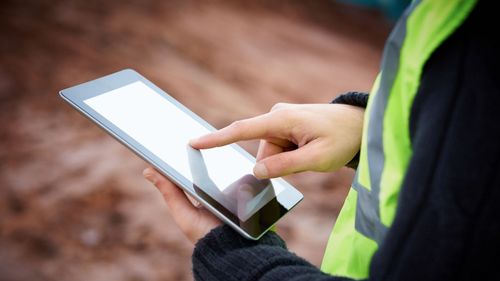
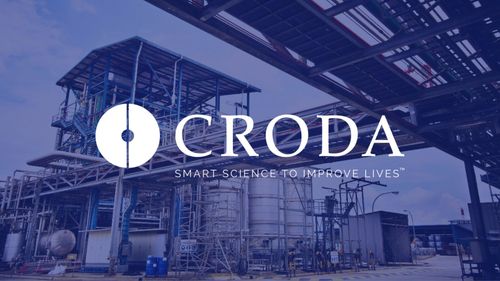
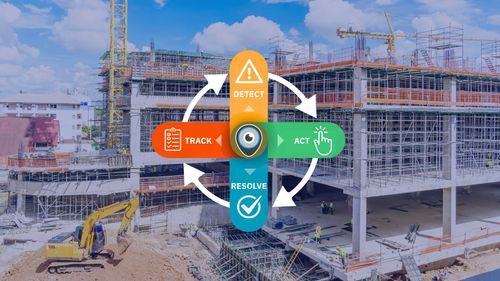