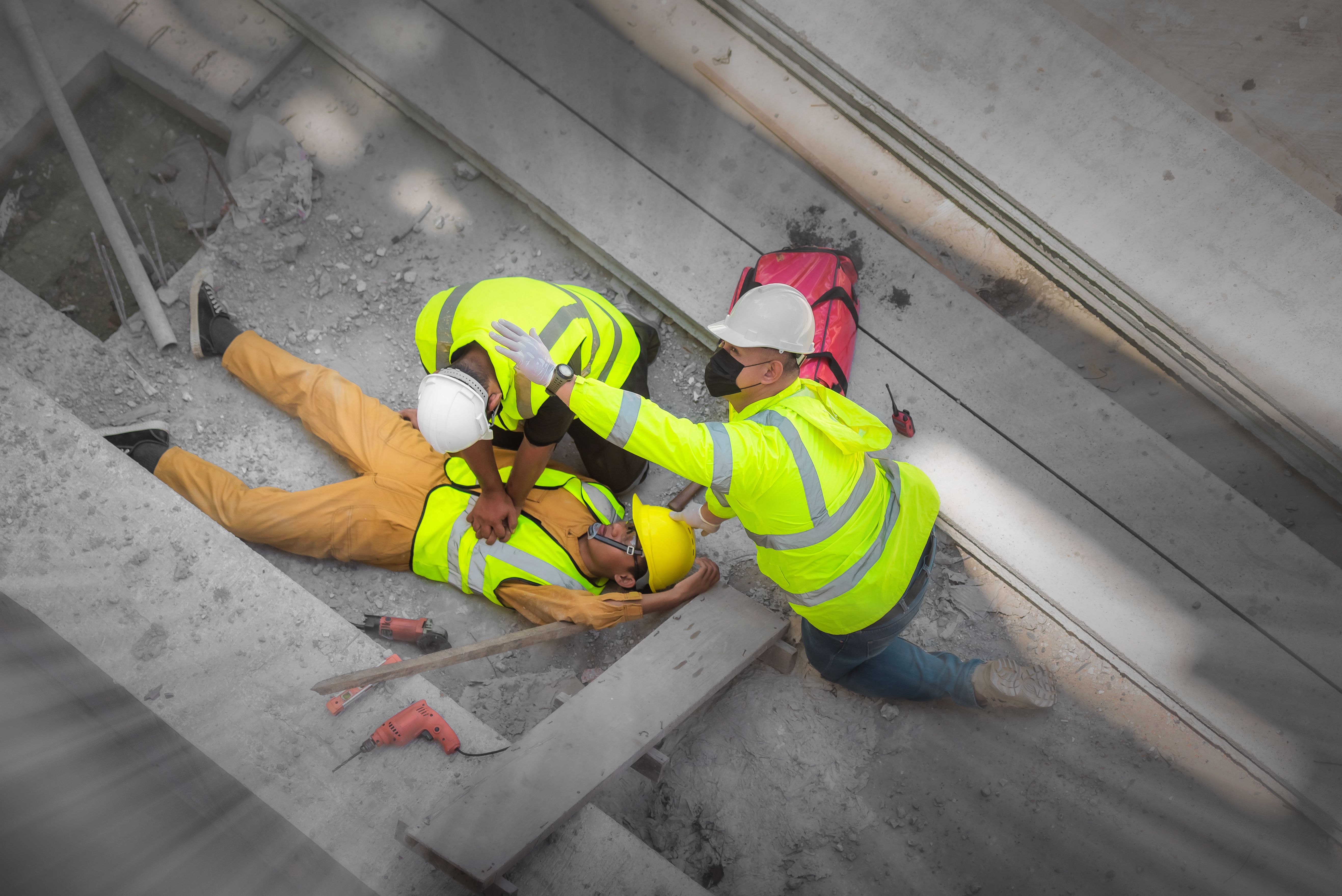
6 Ways Digital Safety Management Systems Can Reduce Workplace Injury and Help Lower Workers’ Compensation Claims
The construction industry in Singapore faced a tragic reality in the first half of 2022, with 10 fatalities and 84 major injuries recorded. Construction, unfortunately, became the leading contributor to workplace fatalities and injuries. However, the cost of lives and permanent damage to workers' bodies is not the only concern, workplace injury costs in the United States alone exceed $170 billion each year, and workers' compensation claims for nonfatal falls account for $2.5 billion annually. This should serve as a wake-up call for companies to prioritize safety in their operations, to keep everyone on the team accountable for a safety-first culture and to create a productive and safe work environment, thus reducing fatal workplace accidents and their costly aftermath.
Current Construction and Contractor Trends That Elevate Company’s Risk of Workplace Injuries
Although the construction industry emerges from the pandemic with an overall positive outlook, severe labour shortages continue to plague the industry. In the struggle to attract and retain skilled workers in the every-competitive market, while some businesses are able to hire subcontractors, contractors are forced to tend toward the expanding labour pool of inexperienced workers. When a greater proportion of workers are less qualified or skilled, the margin for error can be greater and the potential for lapses in safety increases. Add to that an ageing workforce, every workplace injury has greater and more costly consequences.
Some common fatal accidents in the construction industry include:
- Falls from height
- Struck-by accidents, such as being hit by a falling object or moving vehicle
- Electrocutions
- Caught-in/between accidents, such as being trapped by collapsing structures or equipment
- Asphyxiations, due to lack of oxygen or toxic fumes.
According to the latest Singapore National Workplace Safety and Health (WSH) Report 2022, the most common fatal workplace accidents in Singapore are made up by Falls from Height and Vehicular Accidents, while over 50% of minor and major injuries in the workplace are due to Slips, Trips and Falls, Falls from Height, and Machinery Incidents.
It was also discovered that construction companies spend on average 3.6% of their budget addressing workplace injuries, significantly higher than the 2.6% average spent on safety training. Individual injury claims cost upwards of USD$30,000, while fatalities cost over USD$1 million. Should construction companies allocate more budget for training, perhaps the necessity for costly claims will reduce significantly.
Cost of Workers’ Compensation Claims
The costs incurred by a firm due to workplace accidents are split into two categories: direct and indirect.
Direct costs
- Higher insurance premiums (the more accidents on your site, the more dangerous your business is perceived and the higher your insurance premium)
- Workers’ medical expenses
- Legal services to manage accident
Indirect costs
- Accident investigation
- Corrective measure implementation
- Damaged equipment repairs
- Loss in productivity (workers numbers down due to injury, workers’ morale low due to fatal accidents, absenteeism due to morale)
- Potential damage to company’s outlook
Workplace accidents not only decrease productivity and result in costly compensatory claims, they also damage a company's Experience Modification Rate (EMR) which can lead to higher insurance premiums and difficulty in competing for profitable projects.
Additionally, according to the Occupational Health and Safety Administration, firms in the United States pay up to USD$1 billion a week in compensation claims, numbers that no firm should be wilfully costing themselves.
How To Reduce Workers’ Compensation Claims in Construction
To reduce workers’ compensation claims in construction, companies need to construct a safety first culture. This includes:
Implement a Digital Safety Management System
Despite the continual changes in safety regulations in the construction industry, some companies are still not utilising a safety management system, causing a potential issue for ensuring compliance with regulations and maintaining the safety of workers on construction sites.
Provide Regular Safety Training and Education
When it comes to safety training, construction companies often don't prioritise due to lack of resources, scheduling challenges, and a lack of understanding of its importance. By not committing to regular safety training, not only do these companies put their workers in harm's way, but they are also risking their own financial security and their standing within the industry.
Conduct Regular Safety Audits and Inspections
Companies in the construction industry might not perform standard safety inspections and audits due to factors like insufficient resources, unawareness of the value of these assessments, prioritizing financial savings over precautionary steps, and a casual approach to safety. Furthermore, some organisations may not be able to figure out how to carry out efficient safety checks, causing them to fail to put the process into action.
Encourage Workers to Report Injuries and Near-misses in Real Time
Fear of retribution and a lack of knowledge about how to report injuries or near misses can make it difficult for workers to come forward. Moreover, without effective systems in place for tracking and reporting incidents, companies cannot be certain of their level of visibility. Furthermore, a corporate culture that does not prioritise safety is a further disincentive for workers to report incidents.
Provide Workers with Necessary Equipment and Resources to Perform their Job Safely
A variety of causes can be attributed to the failure of construction companies to provide the necessary equipment and resources for safe job performance. These may include improper allocation of resources towards safety, lack of understanding regarding the significance of the right gear, and not abiding by safety regulations and directives. Furthermore, the deficiency of an effective safety management system that evaluates and discerns the specific requirements of employees could also be a contributing factor.
Implement a Return-to-Work Program
With limited resources, stringent budgets, and a general unfamiliarity with the advantages of a return-to-work initiative, many construction firms have difficulty implementing a productive program that enables injured personnel to recuperate and resume their occupation securely.
How an Effective Digital Safety Management System Can Prevent Workplace Injury and Reduce Costly Claims
In order to help build a work culture with safety at its forefront, here are 6 ways how an effective digital safety management system, like the Hubble Safety Management System with its extensive module offerings, can help you prevent workplace injury and reduce costly claims.
1. Ability to track and analyse incidents as well as near misses and incident responses
A comprehensive and data-driven view of all activities on site in the Dashboard module, providing summaries of all safety issues and procedures ongoing on a project.
Image: Dashboard overview of safety inspections
2. Ability to perform root cause analysis
Digital logs of all workplace accident reports are processed by the Safety Inspection module to generate trend data on accident causes.
3. Tools for benchmarking, reporting, and trend-spotting for improvement
Alerts to abnormalities in project sites, identify unsafe conduct of workers and contractors, and create benchmarks for future projects through data analysis in the Dashboard Module.
4. Data collection and management for OSHA inspections
The Equipment Inspection module manages licensing, repair scheduling and certification of all equipment on site for ease of maintenance and assignment to works, which ensures maximum accountability for safety reporting.
Image: Details and certification in Equipment Inspection Module
5. Aid in identifying & incorporating behaviour-based safety training based on trends
The Incident Management & Lesson Learnt module connects teams and disseminates incident reports and insights to all staff, allowing managers to share lessons learnt and align the team on steps to improve safety moving forward.
6. Ability to notify contractors about safety issues in real time
Hubble allows for remote management of all modules, alerting managers of any safety issues immediately and even allowing users to conduct safety inspections on the go.
Elevate Construction Safety with Hubble today
Construction safety technology is also becoming more advanced, and companies are using access control & compliance technologies, mobile devices and cloud-based mobile applications, and data management and analytics to improve safety on their worksites. By implementing these strategies, companies can prevent accidents on construction sites, reduce the number of workers’ compensation claims and improve their overall safety performance.
In conclusion, construction is a high-risk industry that is constantly evolving. Companies are at an elevated risk for workplace injuries and compensation claims. To reduce workers’ compensation claims in construction, companies must construct a safety first culture - Zero compromise towards safety means zero lives lost. Elevate your Safety Management with Hubble today. Ensuring a robust safety management process is crucial to saving lives and reducing cost spent on workplace injury claims.
Share this article
Explore Related Content
Stay up to date with our latest news features!
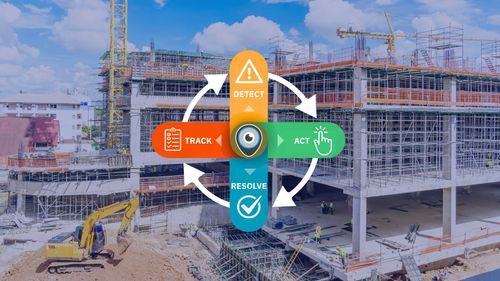
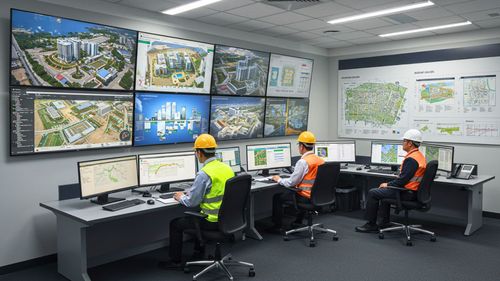
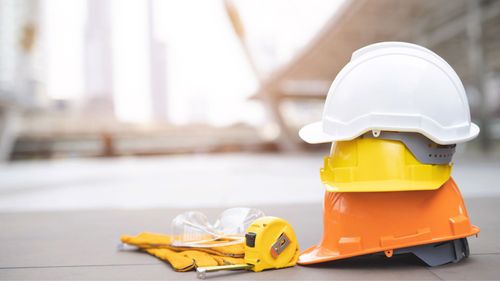