The construction sector remained the largest (26%) contributor to fatal and major injury incidents in the first half of 2024, according to the Ministry of Manpower’s (MOM) Workplace Safety and Health Report (January to June 2024). The MOM plays a crucial role in advocating for workplace safety through initiatives like nation-wide Safety Time Out (STO), a structured pause in operations designed to reassess and reinforce safety protocols. This initiative is crucial for reinforcing safety measures, engaging with workers, and addressing any potential hazards that may compromise workplace safety. This article explores the significance of Safety Time Outs, particularly in light of recent trends in fatal workplace safety incidents, and how technology can be utilised for real-time reporting and inspections during a Safety Time Out.
What is "Safety Time Out" (STO)
A Safety Time Out is a planned event where companies temporarily halt their regular work activities to focus on reviewing and improving workplace safety measures. During this period, management engages with site teams to discuss safety protocols, address specific concerns, and implement necessary changes. The objective is to create a culture of safety awareness and vigilance among all workers.
Importance of Safety in the Construction Industry
Construction sites are inherently hazardous environments, often characterised by heavy machinery, high elevations, and complex operations. Between July and October 2024, construction-related deaths doubled compared to the first half of the year, with 10 workers losing their lives during this period. This alarming trend has prompted authorities to emphasise the need for immediate action to curb complacency and reinforce safety standards. The upcoming festive season further complicates matters as companies may rush to meet deadlines, potentially compromising safety protocols. The recent call for construction companies to conduct a Safety Time Out at any time between 8 to 22 November 2024, underscores the critical nature of this issue.
Recent Fatal Incidents in the Construction Sector
The Ministry of Manpower (MOM) reported that from January to June 2024, 19 workplace deaths occurred across all industries in Singapore, an increase from 14 deaths during the same period in 2023. Vehicular incidents were the top cause, followed by falls from height, and the collapse or breakdown of structures and equipment. The Multi-Agency Workplace Safety and Health Taskforce (MAST) has further strengthened WSH standards in the Construction sector with additional Safety Accountability, Focus and Empowerment (SAFE) measures implemented in early to mid-2024. These include enhanced WSH requirements for public sector construction and construction-related projects (implemented in April 2024), and mandatory video surveillance systems for construction worksites with contract values of $5 million and above (implemented in June 2024).
The construction sector has witnessed several tragic incidents recently. From July to October 2024 alone, 10 fatalities were reported in the construction sector. This increase from 5 deaths in the first half of the year indicates a trend that necessitates immediate intervention. Such incidents are not isolated; they reflect broader systemic issues within the industry that require urgent attention.
- 30 October 2024: A 46-year-old Thai construction worker was fatally struck by a concrete mixer truck at a worksite in Marina East Drive. The truck driver was arrested for causing death by a negligent act.
- 21 October 2024: A 55-year-old Chinese construction worker died when a steel gate frame fell on him at a worksite in Yishun.
- 18 October 2024: A 46-year-old Chinese worker died in hospital from serious head injuries after he was hit by a falling steel bar at a Tuas construction site.
- 11 October 2024: A 38-year-old Bangladeshi construction worker was killed after being struck by a precast concrete drain channel being lifted by an excavator at a Housing and Development Board (HDB) BTO project site along McNair Road.
- 29 September 2024: A 44-year-old Bangladeshi worker was fatally struck by a collapsing steel structure during lifting operations at the Resorts World Sentosa construction site.
- 17 September 2024: Two workers lost their lives due to a heavy machinery accident at a North-South Corridor construction site along Lentor Avenue while assembling a winch drum.
- 28 August 2024: A 35-year-old construction worker from China died on the spot after he was knocked down by a reversing dump truck at a worksite in Changi.
- 16 August 2024: A 40-year-old Bangladeshi worker died after he was struck by a steel frame structure, which fell during a crane lifting operation at a worksite in Pioneer.
- 1 August 2024: A 42-year-old Bangladeshi worker died three days after he was struck by a galvanised iron pipe that fell from the fifth storey of a building under construction in Jurong.
Several factors contribute to the rising number of incidents in construction. These include lapses in adherence to safety protocols, inadequate training for workers, and insufficient oversight by management. The MOM has identified complacency as a significant factor leading to these tragedies. In response to the rising fatalities, MOM has urged construction firms to implement a Safety Time Out at any time from 8 to 22 November 2024. This initiative aims to allow companies to pause operations and critically assess their safety practices to prevent further incidents. Collaborating with various industry associations, MOM aims to create a unified approach towards enhancing safety standards across all construction sites. This collaboration includes intensified inspections and stricter penalties for non-compliance with safety regulations.
Objectives of Safety Time Out (STO)
The primary goal of implementing a Safety Time Out is to pause regular operations and allow senior management to engage directly with site teams and workers. This engagement fosters open communication about safety concerns and reinforces existing safety protocols. During a Safety Time Out, senior management must actively participate in discussions with on-site workers. This interaction helps bridge the gap between management policies and ground-level realities, ensuring that safety measures are practical and effective.
The STO provides an opportunity for companies to critically assess their current safety protocols. By reviewing these measures in light of recent incidents, organisations can identify weaknesses and implement improvements. Each Safety Time Out should focus on addressing specific issues that have led to recent fatalities or near misses. For instance, if falling objects have been identified as a significant risk factor, targeted strategies can be developed during this safety timeout.
Key Focus Areas During Safety Time Out (STO)
To effectively address the rising number of incidents, companies should focus on specific identified areas of concern based on recent incidents during their Safety Time Outs. The task force emphasises three primary areas of concern during this Safety Time Out:
- Falling Objects: Addressing risks associated with overhead work.
- Vehicular Safety: Implementing best practices for managing vehicle-related hazards on site.
- Safe Lifting and Rigging Activities: Establishing guidelines for safe equipment use and handling.
1. Falling Objects
Falling objects remain one of the leading causes of injuries and fatalities on construction sites. According to MOM data, many incidents could have been prevented through better securing practices. To mitigate risks associated with falling objects:
- Implementing proper storage techniques for materials.
- Ensure all materials are stored securely.
- Use appropriate barriers or nets where necessary.
- Using protective equipment such as hard hats.
- Conduct regular inspections to identify potential hazards.
2. Vehicular Safety
Vehicular accidents account for a significant number of fatalities in construction. Common causes include inadequate traffic management plans and lack of proper training for vehicle operators. Effective traffic management plans should include:
- Clearly marked pathways for vehicles and pedestrians.
- Designated areas for loading and unloading materials.
- Implementing strict speed limits on site.
- Regular training sessions for workers on safe vehicular operations.
3. Safe Lifting and Rigging Activities
Lifting operations are inherently dangerous if not conducted properly. Ensuring that all personnel involved are adequately trained is essential for preventing accidents related to lifting activities. Best practices for safe lifting include:
- Conducting thorough equipment checks before use.
- Using appropriate lifting techniques.
- Ensuring that all team members are aware of their roles during lifting operations.
Steps for Conducting an Effective Safety Time Out
To ensure that Safety Time Outs are effective, companies should follow a structured approach:
1. Preparation and Planning
Before initiating a Safety Time Out, thorough preparation is essential. This includes defining the scope and objectives of the time out.
- Define Objectives: Clearly articulate what the organisation aims to achieve during the STO. This could include reviewing specific incidents, addressing identified risks, or enhancing overall safety culture.
- Appoint Leadership: Designate a lead person or team responsible for facilitating the STO. This should include representatives from management, safety personnel, and frontline workers to ensure diverse perspectives.
- Gather Resources: Collect relevant data on past incidents, including near misses and identified hazards, risk assessments, and current safety protocols to inform discussions.
2. Communication
Effective communication is vital for a successful Safety Time Out.
- Notify All Employees: Inform all staff about the upcoming STO well in advance. Use multiple channels such as emails, meetings, and posters to ensure everyone is aware.
- Encourage Participation: Foster an inclusive environment where all employees feel comfortable sharing their concerns and suggestions regarding safety practices.
3. Conducting the Safety Time Out
The actual execution of the Safety Time Out involves several key activities:
- Pause Operations: Temporarily halt all work activities to focus on safety discussions.
- Facilitate Discussions: Lead a meeting where all stakeholders, including site teams and workers, can voice their concerns about workplace safety. Use guided questions to stimulate discussion:
- What hazards have you observed recently?
- Are there any unsafe practices that need addressing?
- How can we improve our current safety measures?
- Review Past Incidents: Analyse recent accidents or near misses to identify root causes and prevent recurrence.
4. Risk Assessment and Hazard Identification
A critical component of the Safety Time Out is conducting a thorough risk assessment.
- Identify Hazards: Encourage participants to identify potential hazards in their work environment. This could include equipment malfunctions, unsafe work practices, or environmental factors.
- Evaluate Risks: Assess the likelihood and severity of identified hazards to prioritise which issues require immediate attention.
5. Developing Action Plans
Once hazards are identified and assessed, it’s time to develop actionable plans.
- Create Mitigation Strategies: Collaboratively develop strategies to eliminate or control identified risks. This may involve:
- Updating training programs
- Modifying work processes
- Implementing new safety equipment or technology
- Assign Responsibilities: Clearly outline who will be responsible for implementing each action item and establish timelines for completion.
6. Documentation
Proper documentation is essential for accountability and future reference.
- Record Findings: Document all discussions, identified hazards, and action plans developed during the STO.
- Maintain Records: Keep records accessible for review during future safety audits or inspections.
7. Follow-Up Actions
After the Safety Time Out concludes, follow-up actions are crucial to ensure that improvements are made.
- Monitor Implementation: Regularly check on the progress of action items assigned during the STO.
- Conduct Training Sessions: Provide additional training if new procedures or equipment were introduced as part of the action plan.
- Reassess Risks Periodically: Schedule regular intervals for risk reassessment to ensure ongoing compliance with safety standards.
To ensure an effective STO, remember to plan ahead and schedule the STO well in advance and communicate it clearly to all stakeholders. All stakeholders should be informed about the purpose, schedule, and expected outcomes well ahead of time. Engage all levels by involving both senior management and frontline workers in discussions. Document the findings by keeping detailed records of discussions and actions taken during the STO.
By following these steps, organisations can maximise the effectiveness of their Safety Time Outs while fostering an environment dedicated to continuous improvement in workplace safety.
Utilising Technology for Real-Time Reporting and Inspections
Technology can play a vital role in enhancing safety during STOs:
- Use mobile applications for real-time reporting of hazards.
Mobile applications allow workers to report hazards instantly, ensuring that safety issues are addressed promptly during Safety Time Outs. - Implement digital checklists for inspections.
Digital checklists can be used to standardise the safety review process, ensuring that all necessary precautions are considered during the Safety Time Out. - Utilise software solutions that facilitate communication between teams.
Using software solutions can facilitate better coordination among teams during Safety Time Outs, ensuring everyone is informed about current safety measures and remains on everyone's radar.
Integrated Construction Management Software Enhances Safety
Integrated construction management software plays a vital role in supporting Safety Time Outs through various features:
- Real-Time Data Tracking and Reporting Capabilities: Allows for immediate identification of potential hazards based on live data from worksites.
- Digital Inspection Tools: Streamlines the process of conducting inspections while ensuring compliance with safety regulations.
- Automated Incident Reporting Systems: Facilitates swift reporting and analysis of incidents, enabling organisations to learn from past mistakes.
- Customisable Safety Checklists and Workflows: Ensures that all necessary safety protocols are followed consistently across different projects.
These technological advancements empower organisations to enhance their safety practices effectively while maintaining operational efficiency.
Benefits of Conducting a Safety Time Out (STO)
Enhanced Safety Awareness and Adherence to Safety Protocols Among Workers
Regularly scheduled STOs help cultivate a culture where safety is prioritised by all team members.
Reduction in Workplace Accidents and Associated Costs
By reinforcing safety practices through STOs, companies can significantly reduce the incidence of accidents, leading to lower insurance costs and fewer disruptions.
Improvement in Overall Safety Culture Within Organisations
A proactive approach towards safety fosters an environment where employees feel valued and responsible for their own well-being as well as that of their colleagues.
Best Practices for Effective Safety Time Outs (STO)
To maximise the effectiveness of Safety Time Outs, consider these best practices:
- Involve All Levels of Staff: Ensure participation from management down to frontline workers for comprehensive insights into safety issues.
- Create a Non-Punitive Environment: Foster an atmosphere where employees feel safe reporting issues without fear of repercussions.
- Utilise Safety Time-Out Checklists: Implement safety time out checklists for conducting STOs to ensure all necessary steps are followed systematically.
- Leverage Technology: Use digital tools, e.g. Hubble Safety Management System, for real-time reporting of hazards and tracking action items post-STO.
Conclusion
Safety Time Outs is crucial for improving construction safety standards amidst rising incidents within the sector. These initiatives provide an opportunity for organisations to pause operations temporarily, reflect on current practices, engage with workers meaningfully, and reinforce vital safety protocols.
As we approach high-risk periods such as the festive season, it is important that construction companies prioritise these safety initiatives within their operational schedules. Protect your workforce and contribute positively to the overall reputation and success of your operations. By fostering a culture dedicated to workplace safety, you can significantly mitigate risks associated with common hazards while ensuring compliance with industry regulations.
Read more: How Digital Safety Management Systems Can Reduce Workplace Injury
Share this article
Explore Related Content
Stay up to date with our latest news features!
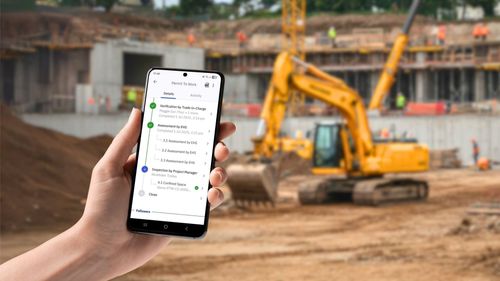
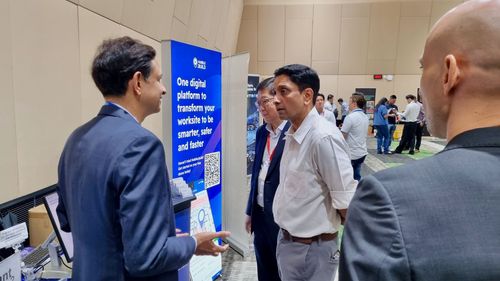
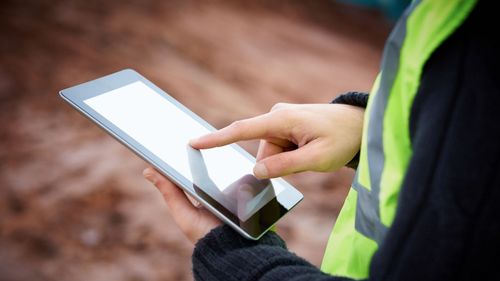