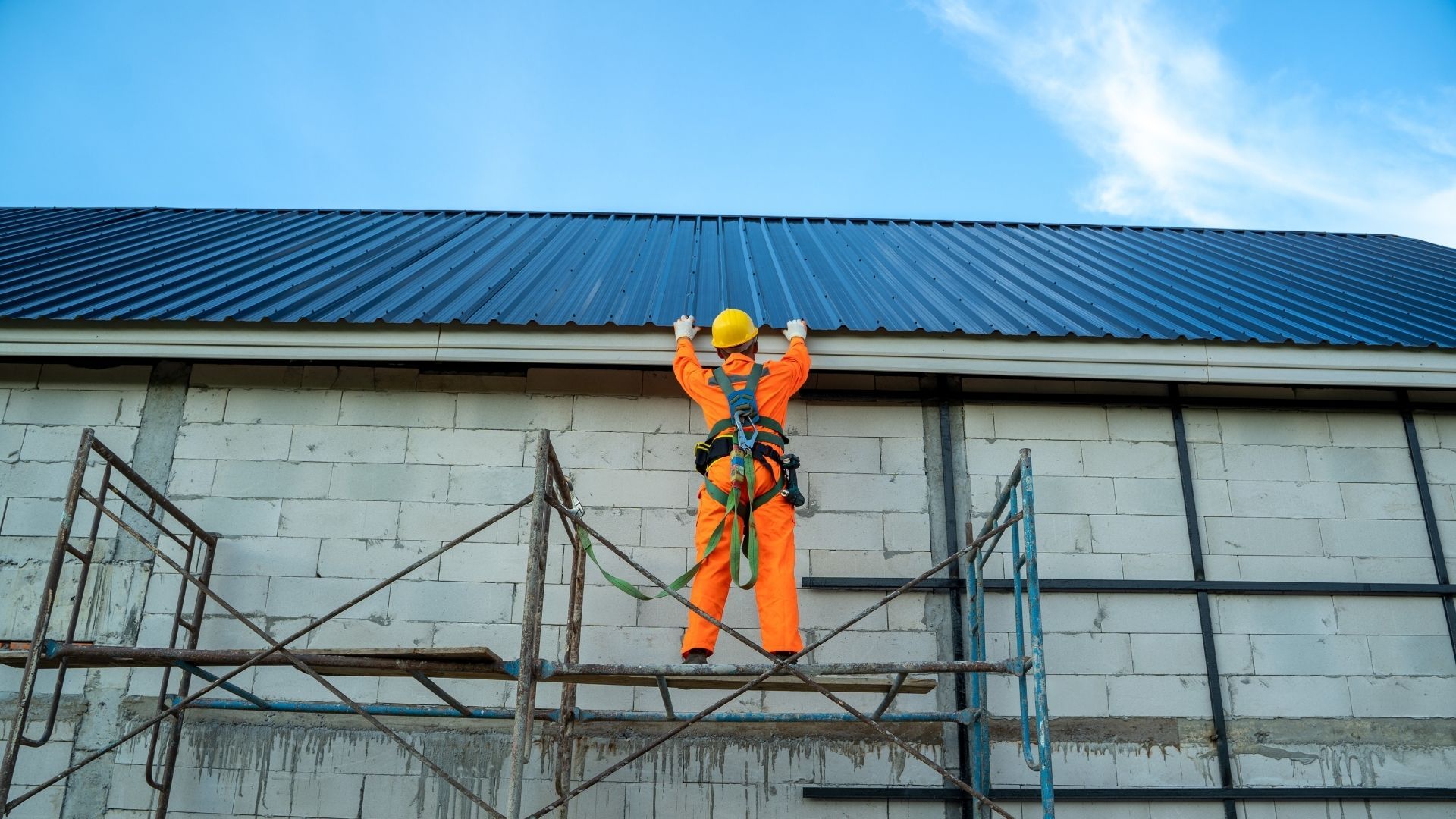
WSH Work at Heights Regulations in Singapore: Guide for Safety and Compliance
Work at Heights regulations play a crucial role in ensuring the safety of workers who perform tasks at elevated heights. Singapore has recognised the importance of implementing Work at Heights regulations to safeguard workers and minimise the risks associated with working at height in various industries, such as construction, maintenance, and cleaning. These regulations play a pivotal role in fostering a safer workplace environment, reducing accidents, injuries and fatalities that may occur due to falls from height.
Workplace Safety and Health (WSH) regulations compliance is crucial in the fast-paced, constantly changing environment of today. Businesses must understand the need of creating a safe and healthy work environment in order to protect the lives and wellbeing of employees as workplace accidents and health risks continue to pose serious threats.
This article aims to spotlight the significance of Work at Heights regulations in Singapore, by detailing the crucial safety measures and legal requirements. Understanding and following these requirements makes companies compliant with Singapore's strict safety regulations while also ensuring the safety of employees and reducing potential dangers.
What is Work at Height
Work at height refers to working in elevated locations, such as rooftops, scaffolding, towers, and various other structures where individuals need to stand, sit, or carry out tasks at certain heights from the ground. Work at height means any task or activity carried out at a certain elevation that involves a risk of falling and causing injury.
According to the recent WSH National Statistic Report (Jan to Jun 2023), falls from height incidents accounted for one of the major causes of total workplace fatalities and injuries in Singapore. These incidents have been attributed to various factors such as lack of proper safety training, failure to implement safety regulations, and inadequate or incorrect usage of equipment. These statistics underscore the urgency and critical importance of comprehensive safety practices and ongoing education in preventing and minimising work at height accidents in the construction and related industries.
The Work at Heights regulations have been put in place to protect workers' safety and wellbeing since working at heights exposes them to a number of risks and hazards. These laws have serious penalties and repercussions for both businesses and employees who violate them. In addition to causing serious injuries or even fatalities, it can also result in legal obligations, reputational harm, and financial hardships. Therefore, it is crucial that companies and employees engaged in work at height activities must abide by these laws, putting in place strong safety measures, offering adequate training, and regularly conducting inspections to ensure compliance. By prioritising compliance, organisations can safeguard their employees, reduce the occurrence of accidents, and foster a culture of safety that contributes to a productive and responsible working environment.
Overview of WSH Work at Heights Regulations in Singapore
Singapore recognised the need for comprehensive safety measures and guidelines in the construction and maintenance industry, particularly pertaining to working at height. In Singapore, the regulatory authority responsible for overseeing work at height guidelines is the Ministry of Manpower (MOM). MOM plays a critical role in ensuring the safety and well-being of workers engaged in tasks conducted at heights, such as construction work or maintenance operations. They meticulously develop and enforce rules and regulations, providing comprehensive guidelines on risk assessment, safety measures, proper equipment usage, and adequate training for all relevant personnel.
MOM introduced the Workplace Safety and Health (Work at Heights) Regulations in 2013, which was revised in 2014 to enhance safety standards further. These regulations aim to prevent falls, protect workers, and ensure the implementation of proper safety measures when working at height. The WSH (Work at Heights) Regulations require employers, self-employed individuals, and principals to implement necessary work-at-height control measures to prevent falls or mitigate the consequences if falls occur. The regulations lay out the responsibilities and duties of various parties involved in work at height activities.
The key provisions in the regulations are:
- Implementation of the Fall Prevention Plan (FPP) in accordance with any Approved Code of Practice issued by the Workplace Safety and Health (WSH) Council
- Implementation of the Permit-to-Work (PTW/ePTW) system to ensure all safety measures are in place before any hazardous Work At Height (WAH) can commence
- Training requirements for Workers, Supervisors and other WAH personnel to ensure effective conduct and oversight of work performed at heights
- Implementation of safety measures while working on roof, near fragile surfaces and by using the industrial rope access system
These regulations emphasise the importance of using proper fall protection systems, such as guardrails, safety nets, and personal protective equipment (PPE) like harnesses and anchorage points, when working at height. These safety measures should be of approved standards and regularly inspected and maintained.
In addition to the Work at Heights legislations, other relevant guidelines and codes of practice should also be considered:
- Code of Practice for Working Safely at Heights
- Code of Practice on Workplace Safety and Health (WSH) Risk Management
- WSH Guidelines on Working Safely on Roofs
- WSH Guidelines on Anchorage, Lifelines and Temporary Edge Protection Systems
- WSH Guidelines on Personal Protective Equipment for Work at Heights
Over the years, Singapore's work at heights regulations have been continually evolving to address emerging challenges and incorporate technological advancements, reinforcing the nation's commitment to creating a safer working environment. With an unwavering commitment to workplace safety, MOM continuously collaborates with industry stakeholders to raise awareness and foster a culture of prevention, ensuring that Singapore maintains the highest standard of safety in all work at height activities.
Responsibilities of Employers and Management
Employers play a vital role in creating a safe and secure working environment for employees involved in elevated tasks. They are responsible for comprehensive risk assessments and developing robust safety protocols before any work at height activities are commenced. This includes identifying hazards, evaluating risks, and implementing work at height control measures to eliminate or minimise the risks.
Employers must also supply appropriate personal protective equipment (PPE) and regularly inspect and maintain all equipment used for working at height. This includes the use of safety harnesses, helmets, guardrails, and other protective measures.
Employers need to provide adequate training and supervision to all employees engaged in work-at-heights tasks. Employers are also required to engage competent personnel or contractors who possess the necessary skills, knowledge, and experience in working at height. Employees should be competent and knowledgeable in safe work procedures, proper handling of equipment, and emergency response protocols. Regular refresher courses should be conducted to ensure the continuous development of employees' skills and knowledge.
It is crucial to stay updated on any amendments or new regulations introduced by MOM and the WSH Council. Regular compliance checks, audits, and inspections should be conducted to ensure ongoing adherence to the legislative requirements. Employers should promote safety awareness, accountability, and continuous improvement in order to promote a culture of safety. Employers can show their commitment to ensuring the well-being and protection of their workforce by carrying out these obligations.
What is Fall Prevention Plan (FPP)
A fall prevention plan (FPP) is a site-specific plan to eliminate or reduce the risk of falls. As an occupier of a worksite, shipyard or premise for bulk storage of toxic or flammable liquid, you are required to implement an FPP in your workplace where WAH is carried out. You are also required to implement an FPP if your factory:
- Manufactures or processes petroleum and petrochemicals, and their products
- Manufactures chlorine, fluorine, hydrogen fluoride or carbon monoxide
- Manufactures synthetic polymers
- Manufactures pharmaceutical products or their intermediates
- Manufactures semiconductor wafers
- Employs 50 or more people
Your FPP should include (but not limited to) the following components:
- Fall prevention policy
- Responsibilities
- Risk management and work at height control measures
- Safe work procedures
- Use of PPE
- Inspection and maintenance
- Training
- Incident investigation
- Emergency response
What is Permit-to-Work (PTW) System
A PTW system is required for Work at Height (WAH) where a person could fall from a height of more than 3 metres, including falling into depths. Such work activities are deemed as hazardous WAH under the regulations. Under the WSH (WAH) (Amendment) Regulations 2014, which came into effect from 1 May 2014, the PTW regulatory requirements apply only to workplaces defined as Factories, as defined under the Workplace Safety and Health (WSH) Act, instead of all workplaces.
The process for the PTW system involves the following stages:
Stage 1: Highlight Potential Hazards
In accordance with the PTW requirements, workers identify potential hazards and implement all essential safety measures, under the supervision of their supervisors. Work is not permitted to start until Stage 4.
Stage 2: Application of Permit
When all of the conditions in the PTW are met, the supervisor requests authorisation to start work and submits the PTW application to the WAH Safety Assessor. The supervisor must state in the PTW that a risk assessment for WAH has been completed and the safety control measures that will be put into place.
Stage 3: Evaluation of Permit
Together with the supervisor, the WAH Safety Assessor visits the work site to assess and confirm that all safety requirements outlined in the PTW have been met. The Assessor might suggest additional actions. After completing this, the Assessor should sign the PTW form and send it to the Authorised Manager.
Stage 4: Approval of Permit
The Authorised Manager approves and issues the PTW when he/she is satisfied that the following requirements have been met:
- All potential hazards and risks for the work have been adequately addressed.
- All reasonably practicable safety measures have been taken.
- All persons involved in the work have been informed of the work hazards and precautions.
- No incompatible work is carried out at the same time and at the location of the hazardous WAH.
Work should start only after the permit has been approved. The Authorised Manager, Safety Assessor and Supervisor must monitor the work continually to ensure that it is executed according to the permit.
For WAH where the risk of falling more than 3 metres have been mitigated through adequate and effective edge protection, a PTW may not be required, unless the responsible person (employer or the principal) deemed that a PTW should still be implemented. Such WAH situations where a PTW may not be required, include but are not limited to the following:
- Working on a flat roof with a perimeter parapet wall of at least 1 metre in height, and no openings or open sides where a person may fall
- Working on a mezzanine with safe and proper stair access and effective barricade around the mezzanine perimeter to prevent falls
- Working within the properly barricaded mobile elevated work platform (with the appropriate PPE anchored to designated anchor points at all times)
Having an electronic Permit To Work (e-PTW) software will help to streamline and digitise PTW and track safety data in real-time to enable the identification of urgent issues quickly. Unlike the paper-based work authorization process, which typically uses paper printouts that must be manually signed off by management for approval, this electronic process reduces paperwork and the time required for the submission and approval process. Benefits of e-PTW over traditional paper-based system:
- Improve coordination and efficiency through real-time notifications.
- Better traceability and accountability of PTW with audit trail.
- Easy identification of incompatible works.
- Full visibility of PTWs via dashboards.
- Remove need to rewrite documents when PTW needs to be extended or re-issued.
Read more: ePTW vs Manual PTW
Selecting and Inspecting Work at Height Equipment
Working at heights demands careful consideration of safety measures, and the choice of equipment plays a critical role in ensuring the well-being of workers. Some commonly used equipment includes ladders, scaffolding systems, aerial lifts (such as scissor and boom lifts), suspended platforms, rope access systems, and personal fall protection gear (such as harnesses and safety lanyards). Each of these devices offers distinct advantages and application-specific benefits, tailored to different work environments and tasks. Understanding the purpose, limitations, and proper usage of these equipment types is indispensable in maintaining a safe and productive work environment at elevated levels.
When selecting appropriate work at height equipment, there are several crucial factors to consider to ensure safety and efficiency. First, it is important to carefully assess the nature of the task and the job’s specific requirements. This involves taking into account the required mobility, the work's duration, the height and type of structure. Second, it's essential to understand the rules and safety control measures that apply to working at height. The chosen equipment should meet industry standards and offer sufficient protection from falls and other potential risks. In addition, consideration should be given to the knowledge and experience of the personnel using the equipment. It is crucial to choose equipment that is compatible with the workers' expertise and ability level. The equipment's usability and accessibility must also be taken into account for productivity. Factors like portability, manoeuvrability, and maintenance requirements should all be considered in order to make an informed choice for the specific work at height project.
Regular inspections, maintenance, and certification play a vital role in ensuring equipment safety. This aspect is crucial as it guarantees the well-being of workers who rely on such equipment to perform their tasks. Routine inspections help identify any potential damages or defects that may compromise safety, allowing for timely repairs or replacements. Regular maintenance ensures that the equipment remains in optimal condition, minimising the risk of accidents and enhancing its lifespan. Additionally, obtaining certification for work at height equipment demonstrates compliance with industry standards and regulations, instilling confidence among workers and employers. By prioritising these practices, organisations establish a culture of safety, safeguarding their workforce while fostering productivity and efficiency in their operations.
Work at Height Training and Competency Requirements
Employers or Principals (e.g. main contractors who engage sub-contractors) are required to first provide adequate safety and health training for workers carrying out WAH before they commence work. The training provided must allow the workers to be familiar with:
- WAH hazards
- Safety precautions to be observed with respect to the work performed at heights.
Competent persons are required to carry out the following roles:
- Supervisors of persons carrying out WAH
- Appointed WAH Safety Assessor
- Appointed Authorised Manager
The above competent persons must have sufficient experience and training to perform the work they are required to carry out under the Regulations. The following summarises the key requirements for WAH training for the various personnel under the Regulations.
Workers can attend:
- WSQ Perform Work at Height Course
- formerly known as “Work-At-Height Course for Workers” (WAHW) - WSQ Apply Workplace Safety and Health in Construction Sites (AWSHCS)
- formerly known as “Construction Safety Orientation Course” (CSOC)
Supervisors (personnel who are carrying out supervision over WAH activities) can attend:
- WSQ Manage Work-At-Height Course (MWAH)
- formerly known as “Managing Work-At-Height Course” - WSQ Workplace Safety and Health Management in Construction Industry (WSHMCI)
- formerly known as “WSQ Supervise Construction Work for WSH” (SCWWSH) and “Building Construction Supervisor Safety Course” (BCSS)
WAH Safety Assessor can attend:
- WSQ Manage Work-At-Height Course (MWAH)
- formerly known as “Managing Work-At-Height Course”
Alternatively, registered WSH Officers may be appointed to carry out the duties of WAH Safety Assessor without the need to attend the WAH course for Assessors.
Authorised Manager can attend:
- WSQ Manage Work-At-Height Course (MWAH)
- formerly known as “Managing Work-At-Height Course” - WSQ Manage Workplace Safety and Health in Construction Sites
- formerly known as “Construction Safety Course for Project Managers” (CSCPM)
Having a Workforce Management System allows you to easily match workers’ WAH competency with the right work at height tasks through workforce management.
Benefits of Work at Heights Regulations for Businesses and Workers
Work at heights regulations in Singapore promote a culture of safety within the workplace. Employers are encouraged to prioritise safety as an integral part of their operations, fostering an environment where employees feel secure and valued. Regular inspections and audits help identify potential hazards and ensure compliance with safety standards. The regulations also emphasise the importance of proper training and supervision. Employers are obligated to provide adequate training to workers regarding working safely at height, hazard identification, and proper use of safety equipment. Supervisors play a critical role in overseeing work activities, ensuring adherence to safety protocols, and addressing any safety concerns promptly.
Having a digital safety management system provides numerous benefits, including increased efficiency in safety procedures, improved compliance with regulations, streamlined communication and documentation processes, and easier access to real-time safety data and analytics. By leveraging such digital platforms, companies can enhance safety protocols, minimise risks, and maximise efficiency. From documenting incident reports to electronic PTW, digital platforms provide a seamless and secure ecosystem for managing and reporting work-at-height safety measures.
In conclusion, work at heights regulations in Singapore are of utmost importance to protect the lives and well-being of workers undertaking tasks at elevated heights. It helps to drive a positive impact on employee morale and employer reputation. By establishing comprehensive safety guidelines, educating employers and employees, enforcing compliance, and fostering a culture of safety, these regulations contribute significantly to enhancing productivity, reducing downtime, minimising accidents and promoting occupational safety.
Read also: WSH Construction Regulations in Singapore: A Comprehensive Guide
Share this article
Explore Related Content
Stay up to date with our latest news features!
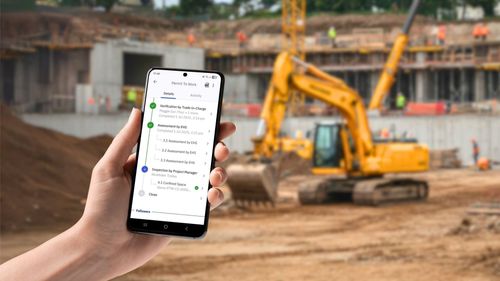
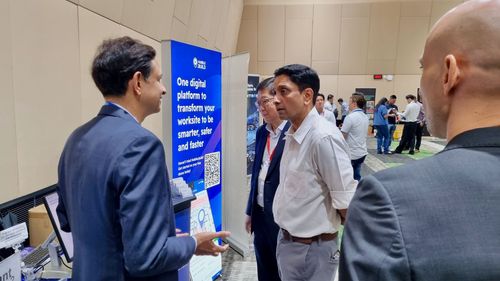
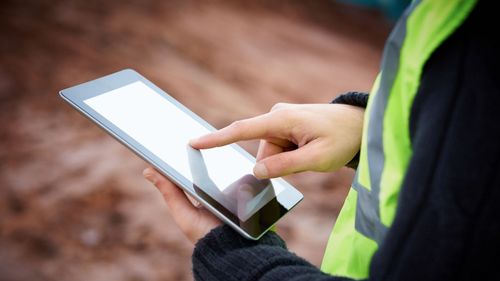