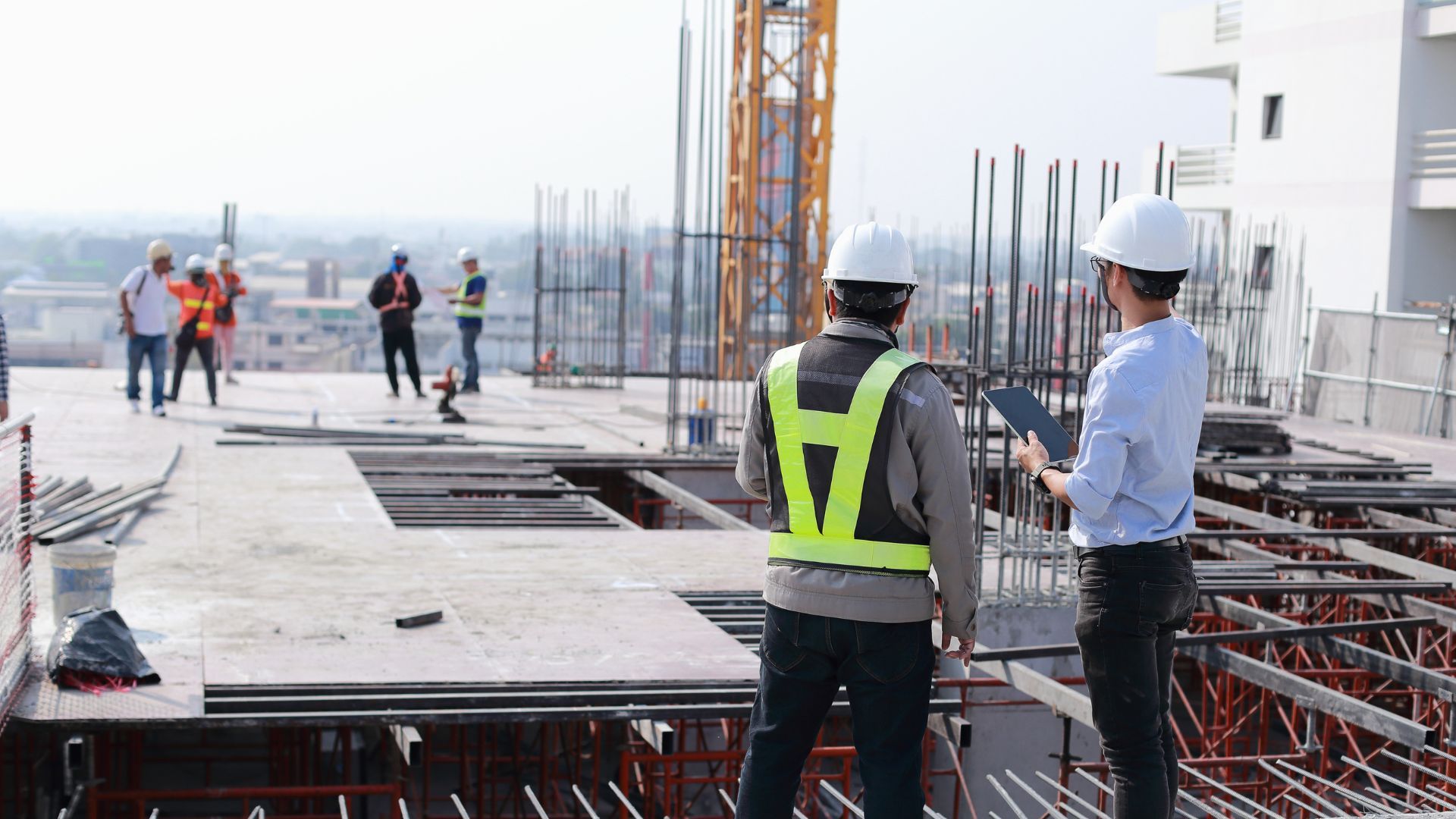
Digital Tools for Inspection and Test Plans (ITP) in Construction Quality
It is crucial to ensure quality and compliance through effective Inspection and Test Plans (ITPs). Traditional methods of managing ITPs can be cumbersome and prone to errors. Integrated quality management offers innovative solutions that enhance the efficiency, accuracy, and collaboration involved in developing and executing ITPs. This article delves into how digital transformation can enhance your approach to quality management in construction.
What is an Inspection and Test Plan (ITP) in Construction
An Inspection and Test Plan (ITP) outlines the specific inspections and tests required during various stages of a construction project to ensure compliance with quality standards and specifications. ITP typically includes details such as inspection types, acceptance criteria, responsible parties, and timelines. Effective ITPs help mitigate risks, reduce rework, and ensure that projects meet regulatory requirements.
Typical Components of an Inspection and Test Plan
1. Project Details
- Project Name: The title of the project.
- Location: Where the project is being executed.
- Client Information: Details about the client or owner of the project.
2. Scope of Work
- A clear description of the work involved, including materials, processes, and systems that will be inspected.
3. Inspection and Testing Requirements
- Types of Inspections: Visual inspections, non-destructive testing (NDT), functional testing, etc.
- Testing Methods: Specific methods to be used for testing materials or systems.
4. Acceptance Criteria
- Defined standards that must be met for each inspection or test to be considered successful. This could include industry standards (like ASTM or IS codes) or project-specific criteria.
5. Responsibilities
- Clear definition of roles and responsibilities for all parties involved in the inspection process, including contractors, subcontractors, and third-party inspectors.
6. Schedule of Inspections
- A timeline indicating when each inspection or test will occur relative to the project schedule.
7. Documentation Requirements
- Details on how inspection results will be recorded, reported, and archived for future reference.
8. Non-Conformance Procedures
- Steps to follow if a test fails or if an inspection does not meet the acceptance criteria, including corrective actions.
Purpose of an Inspection and Test Plan
- Quality Assurance: ITPs help ensure that all aspects of construction meet predefined quality standards before moving forward.
- Risk Management: By identifying potential issues early through systematic inspections and tests, ITPs mitigate risks associated with defects and non-compliance.
- Regulatory Compliance: Many industries have strict regulations governing safety and quality; ITPs help ensure adherence to these regulations.
- Communication Tool: ITPs serve as a communication bridge between various stakeholders (clients, contractors, inspectors), ensuring everyone is on the same radar regarding quality expectations.
When roles are clearly defined in an ITP, it helps to foster accountability among team members, ensuring that everyone understands their responsibilities regarding inspections and tests. With a streamlined and structured approach to inspections and testing outlined in an ITP, projects can run more smoothly, reducing delays caused by unforeseen issues. The records generated from ITPs can serve as valuable documentation references for future projects or audits, showcasing compliance and quality assurance efforts.
Importance of Inspection and Test Plans in Construction
Inspection and Test Plans (ITPs) are critical documents in the construction industry, serving as a roadmap for quality assurance and compliance.
1. Quality Control Assurance
ITPs provide a systematic approach to ensuring that all aspects of a project meet specified quality standards. By outlining inspection points and acceptance criteria, ITPs help maintain consistency throughout the construction process.
ITPs are instrumental in defect prevention. By identifying potential issues early in the construction phase, ITPs can prevent defects that might otherwise lead to costly rework or delays.
2. Regulatory Compliance
Adherence to standards is a critical aspect of any construction project. Construction projects must comply with various local and international standards, codes, and regulations. ITPs help ensure that all inspections align with these requirements, reducing the risk of legal complications.
ITPs serve as essential documentation during audits and inspections conducted by regulatory bodies. They provide tangible evidence that due diligence has been exercised in maintaining quality throughout the construction process.
3. Enhanced Communication
ITPs facilitate better communication among project stakeholders, including contractors, subcontractors, and clients. By clearly defining roles and responsibilities related to inspections, everyone involved understands their obligations. This clarity helps to minimize misunderstandings and sets clear expectations, leading to a more streamlined workflow.
The structured nature of ITPs also creates an effective feedback loop throughout the project lifecycle. This allows for ongoing feedback and adjustments to be made as necessary, fostering a collaborative environment
4. Risk Management
By outlining specific inspection points and criteria, ITPs help identify potential risks at various stages of the project. This proactive approach allows teams to address issues before they escalate.
In addition to identifying risks, ITPs also incorporate mitigation strategies that prepare teams for potential challenges. These plans often include contingency measures for addressing non-conformance or failures that may arise during inspections. By having these mitigation strategies in place, teams can respond effectively and efficiently, minimizing disruptions and ensuring that quality standards are maintained throughout the project lifecycle.
5. Cost Efficiency
By catching issues early through systematic inspections, ITPs can significantly reduce the costs associated with rework and project delays. Identifying potential problems before they escalate allows teams to address them promptly, minimizing the financial impact that often accompanies late-stage corrections.
Additionally, with clear inspection schedules and criteria, teams can allocate resources more effectively. This structured approach ensures that time and materials are utilized efficiently, reducing waste and improving overall project productivity.
6. Continuous Improvement
ITPs can serve as a repository for lessons learned during inspections. By systematically documenting these experiences, organisations can refine their processes over time, ensuring that past mistakes are not repeated and that best practices are consistently applied.
By analysing inspection results against established criteria, companies can benchmark their performance and identify areas for improvement.
Challenges with Traditional ITP Management
- Manual Processes: Inefficient teams often rely on spreadsheets or paper-based systems to manage ITPs.
- Version Control Issues: Keeping track of multiple versions of documents can result in confusion and miscommunication.
- Limited Collaboration: Stakeholders may struggle to access real-time information, leading to delays in decision-making, rework, and increased costs.
- Data Silos: Information may be scattered across different platforms, making it difficult to analyse trends or generate reports.
Digital Tools for Inspection and Test Plans
The construction industry is increasingly embracing digital solutions to enhance efficiency, accuracy, and collaboration. When it comes to Inspection and Test Plans (ITP), various digital tools can streamline the creation, management, and execution of these plans. Here is an in-depth look at the types of digital tools available and their benefits.
1. Construction Management Software: Comprehensive platforms that integrate various aspects of construction management, including ITPs. Construction management software may includes project scheduling, document management, and real-time collaboration among stakeholders.
2. Mobile Applications: Apps designed for field use allow inspectors to access ITPs on-site, record findings, and share updates instantly. These construction management apps often include offline capabilities, ensuring usability in remote locations.
3. Document Management Systems: Solutions that help organise and store ITP documents securely. Document management system often includes version control, easy retrieval, and sharing capabilities among team members.
4. Quality Management Software: Specialised tools focused on quality assurance processes. Quality management software often provides templates for ITPs, track compliance with standards, and generate reports on inspection outcomes.
5. Collaboration Platforms: Tools that facilitate communication among project teams. These platforms can integrate with ITPs to allow for real-time updates and discussions regarding inspection results.
6. Data Analytics Tools: Solutions that analyse data collected during inspections to identify trends and areas for improvement. These insights can inform future projects and enhance overall quality control practices.
Benefits of Integrated Quality Management Software
1. Centralised Data Management
- Single Source of Truth: Integrated construction management software provides a centralised platform where all stakeholders can access up-to-date ITPs, reducing confusion and ensuring everyone is on the same page.
- Document Management: Easily store and retrieve documents related to inspections, tests, and compliance requirements.
2. Streamlined Workflow Automation
- Automated Notifications: Set up alerts for upcoming inspections or deadlines, ensuring that team members are always informed.
- Task Assignment: Assign responsibilities directly within the digital construction platform, allowing for clear accountability and tracking of progress.
3. Enhanced Collaboration
- Real-Time Updates: With an integrated quality management, teams can collaborate in real time, making it easier to discuss findings, share feedback, and make necessary adjustments to ITPs.
- Mobile Access: Field teams can access ITPs via mobile devices, enabling them to conduct inspections and document results on-site without delays.
4. Improved Reporting and Analytics
- Data Insights: Integrated construction management software includes analytics tools that allow teams to analyse inspection data over time, identifying trends or recurring issues.
- Custom Reports: Generate customisable reports for stakeholders that summarise inspection results, compliance status, and areas for improvement.
5. Compliance Tracking
- Regulatory Compliance: Ensure that all inspections are documented according to industry regulations by using customised compliance checklists within the software.
- Audit Trails: Maintain a comprehensive record of all changes made to ITPs for accountability during audits.
The integration of quality management into the development and execution of Inspection and Test Plans represents a significant step forward in quality management practices. By embracing digital transformation, construction teams can enhance collaboration, streamline workflows, and ultimately deliver projects that meet or exceed quality standards. Leveraging technology is essential for staying competitive and ensuring project success.
Transform Your Quality Management with Hubble Today!
Are you ready to elevate your Inspection and Test Plans and streamline your construction processes? Discover how our integrated construction management software can help you enhance collaboration, improve compliance and gain valuable insights.
👉 Schedule a Demo
Experience firsthand how our innovative digital construction solutions can optimise your quality management practices. Don’t miss out on the opportunity to boost efficiency and ensure project success.
Join the growing number of construction professionals who are embracing digital transformation for a brighter, more efficient future!
Read more: How Integrated Quality Management Enhances Construction Project Success
Share this article
Explore Related Content
Stay up to date with our latest news features!
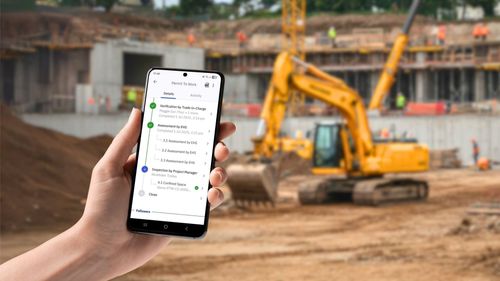
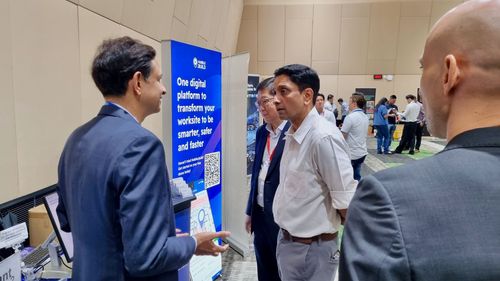
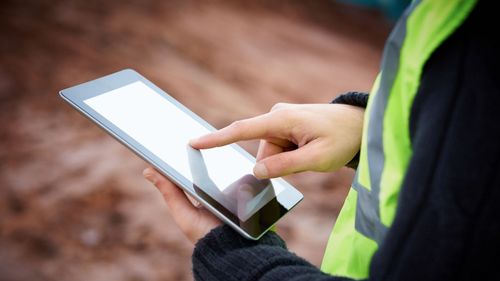