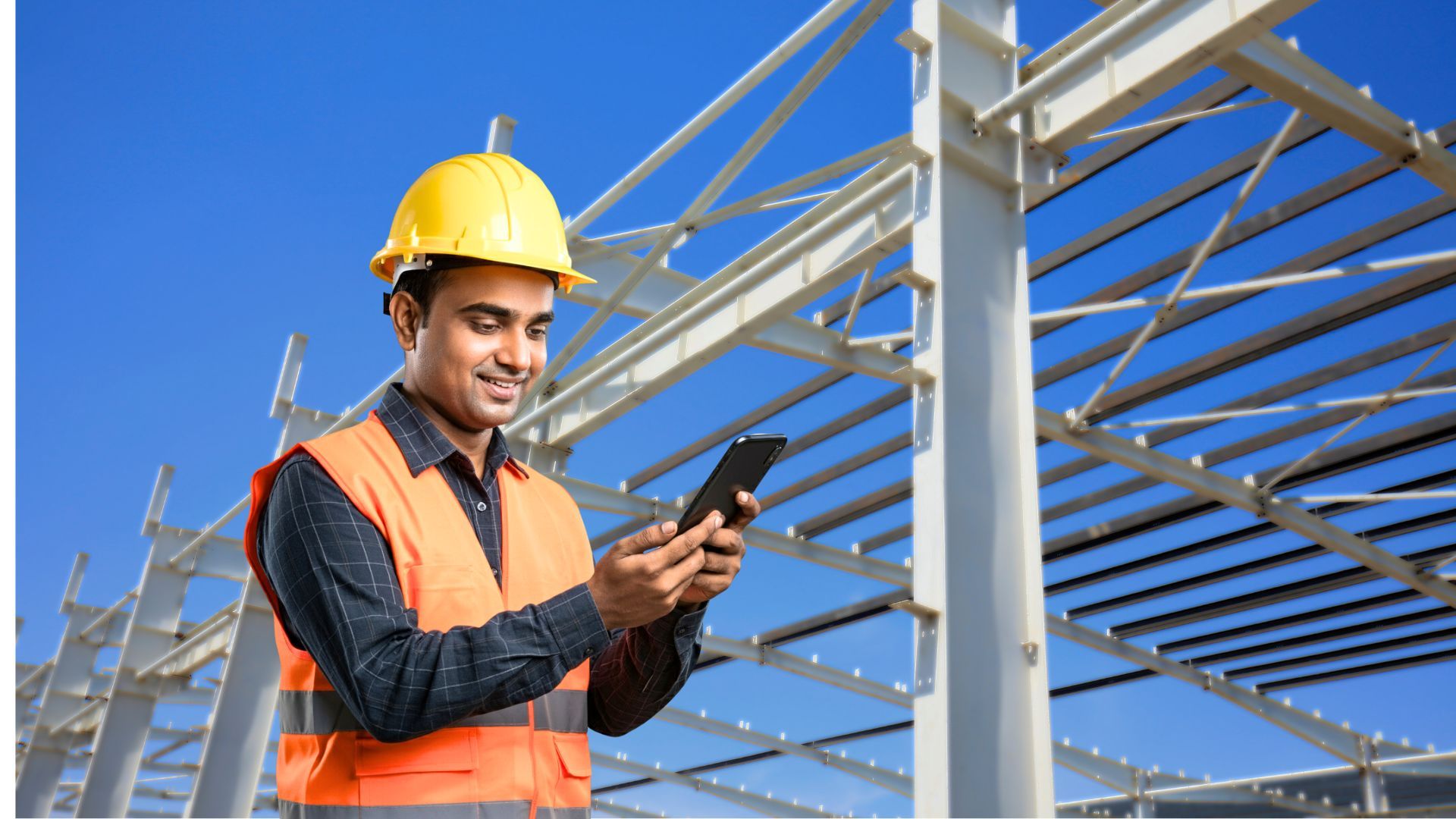
How Integrated Quality Management Enhances Construction Project Success
With increasing competition and rising client expectations, construction companies must adopt innovative strategies to ensure project success. One of the most effective approaches is implementing an Integrated Quality Management System (QMS). This article explores the significance of integrated quality management in construction, its benefits and how technology can facilitate this integration.
What is Integrated Quality Management
Integrated Quality Management refers to a holistic approach that combines various quality management practices into a unified system. It encompasses planning, control, assurance, and improvement processes that are essential for delivering projects that meet or exceed client expectations while adhering to regulatory standards. By embedding quality at every stage of the process, from pre-construction to post-construction, you can reduce defects, minimise rework, and foster a culture of continuous improvement.
- Quality Control Plan (QCP): A QCP outlines the specific quality standards and procedures that must be adhered to throughout the project lifecycle. It includes roles and responsibilities, inspection protocols, and documentation processes.
- Inspection and Test Plan (ITP): This plan details the inspections and tests required at various stages of construction to ensure compliance with quality standards. It specifies when and how these tests will be conducted, as well as acceptance criteria.
- Work Method Statement (WMS): A WMS provides a detailed description of how specific tasks will be performed, including safety measures and quality controls. It serves as a guide for workers to execute their tasks correctly and efficiently.
The integration of Document, Fabrication, Quality and Handover management systems is crucial for seamless project execution. Here are some ways how these systems interact across the various construction phases:
Document Management System: This serves as a centralised repository for all project-related documents, including QCPs, ITPs, and WMSs. It ensures that all stakeholders have access to the latest versions of documents, facilitating collaboration and transparency.
Fabrication Management System: Manages the production of materials and components based on the specifications outlined in the QCP and ITP. By automating fabrication processes, it reduces errors and enhances efficiency.
Quality Management System: Encompasses both Quality Assurance (QA) and Quality Control (QC) processes, such as Non-Conformance Reports (NCRs) to document deviations from established quality standards. The system also utilises checklists during various construction phases to ensure compliance with quality specifications.
Handover Management System: Ensures all quality checks are completed before a project is handed over to clients. This includes inspection reports, which confirm that all work meets contractual obligations before project sign-off.
The Importance of Quality Management in Construction
Quality management is not merely about compliance; it’s about creating value. Here are some key reasons why integrated quality management is crucial in the construction sector:
Risk Mitigation: Construction projects are fraught with risks—ranging from design flaws to material defects. An integrated quality management allows teams to identify potential issues early and implement corrective actions before they escalate into costly problems.
Cost Efficiency: By minimising defects and rework, integrated quality management can significantly reduce project costs. Studies show that organisations with robust quality management practices experience lower operational costs and higher profit margins.
Enhanced Client Satisfaction: Delivering projects that meet quality standards leads to satisfied clients who are more likely to return for future business and recommend your services to others. In an industry where reputation is everything, maintaining high-quality standards is essential.
Continuous Improvement: An integrated quality management fosters a culture of continuous improvement by encouraging feedback and learning from past projects. This iterative process helps organisations refine their practices and enhance overall performance.
Digitising Quality Management Workflows
One way to streamline your quality management processes is through an integrated construction management software solution. By digitising key workflows, you can improve efficiency, reduce costs, and deliver higher-quality projects to your clients. Here are some example workflows:
Quality Assurance Inspection of Material Sources
Before any construction project begins, it's essential to approve and confirm the sources of raw materials. This includes verifying the country of origin for materials like steel, cement, and aggregates, as well as approving the manufacturers of products like tiles and fixtures.
- Approval and Confirmation: Validate the material source and manufacturer credentials.
- Documentation Review: Ensure that all necessary certifications and compliance documents are in place.
This proactive approach helps prevent issues related to material quality that could arise later in the construction process. By digitising this workflow, you can centralise all material source information, automate approval processes, and ensure that only approved suppliers are used across your projects.
Quality Assurance Inspection of Supplier Facilities
Maintaining quality standards extends beyond just the materials themselves. It's also crucial to ensure that your suppliers' facilities meet your required standards for cleanliness, safety, and production processes. By conducting regular spot checks and sampling inspections, you can verify that your suppliers are consistently delivering high-quality products. Digitising this workflow allows you to schedule and track inspections, document findings, and share results with suppliers and project teams in real-time.
Quality Assurance Inspection of Materials at Supplier Facilities
Once you have approved your material sources and suppliers, the next step is to inspect the raw materials and finished products at the supplier's facility before shipping to the project site. This sampling inspection process helps catch any defects or non-conformances early in the supply chain. For finished products like tiles or fixtures, a full inspection is recommended to ensure they meet your specifications before being installed on site. By digitising this workflow, you can standardise your inspection checklists, automate scheduling, and generate detailed inspection reports to share with suppliers and project teams.
Quality Assurance Inspection of Construction Works at Project Site
Another quality assurance is conducting quality inspections of the actual construction work at the project site. This involves inspecting the work at each required phase of completion, such as before pouring concrete, before closing walls, or before installing ceilings.
- Phase Completion Inspections: Conduct inspections at each critical phase to verify adherence to design specifications and quality standards.
- Documentation and Reporting: Maintain detailed records of inspections, findings, and corrective actions taken.
This continuous monitoring not only ensures compliance but also fosters accountability among contractors and subcontractors. By digitising this workflow, you can create standardised checklists for each type of quality inspection, assign inspections to specific team members, and track the status of inspections in real-time. This helps ensure that work is being completed to the required standards and any issues are caught and addressed promptly.
Benefits of a Digital Integrated Quality Management
By digitising workflows using an integrated construction management software solution, companies can streamline their quality management processes, improve collaboration between teams, and deliver higher-quality projects to their clients. The benefits of digitisation include:
Real-Time Monitoring: Visibility into inspection status and quality issues across projects. Digital tools enable real-time tracking of project progress, allowing for immediate identification of issues or delays. This proactive approach helps in maintaining timelines and budget constraints.
Standardised Processes: Establish clear procedures for quality assurance and control across all project phases. Standardisation helps ensure consistency and compliance with industry regulations.
Enhanced Collaboration: Foster better communication between all stakeholders—contractors, subcontractors, suppliers, and clients—through collaborative platforms that facilitate information sharing and feedback.
Improved Quality Assurance: With digitised workflows, quality control measures can be implemented more effectively. Automated alerts can notify teams of upcoming inspections or deadlines, ensuring that no critical steps are overlooked.
Achieve Higher Quality Standards in Construction Projects
Integrating quality management into your construction projects is about achieving excellence in every aspect of the project lifecycle. By adopting a holistic approach to quality management, you can enhance your reputation for delivering high-quality projects on time and on budget, reduce costs associated with rework and defects, mitigate risks, and foster a culture of continuous improvement within your organisation.
At Hubble, we specialise in tailoring integrated construction management solutions designed to help you achieve these goals. Our software empowers teams with real-time insights and collaborative tools that drive efficiency while maintaining high-quality standards.
If you’re interested in learning more about how we can assist you in implementing an integrated quality management solution tailored to your specific needs, please feel free to reach out or schedule a demo. Together, let’s pave the way for excellence in your construction projects!
Share this article
Explore Related Content
Stay up to date with our latest news features!
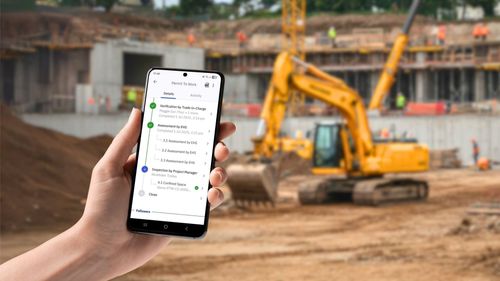
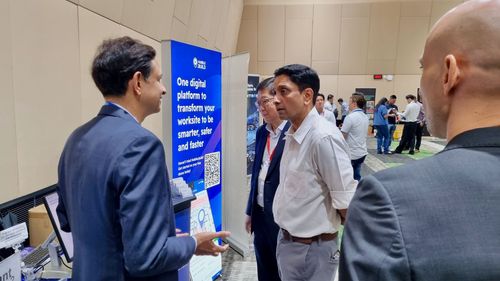
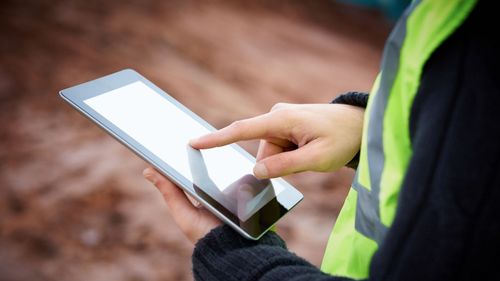