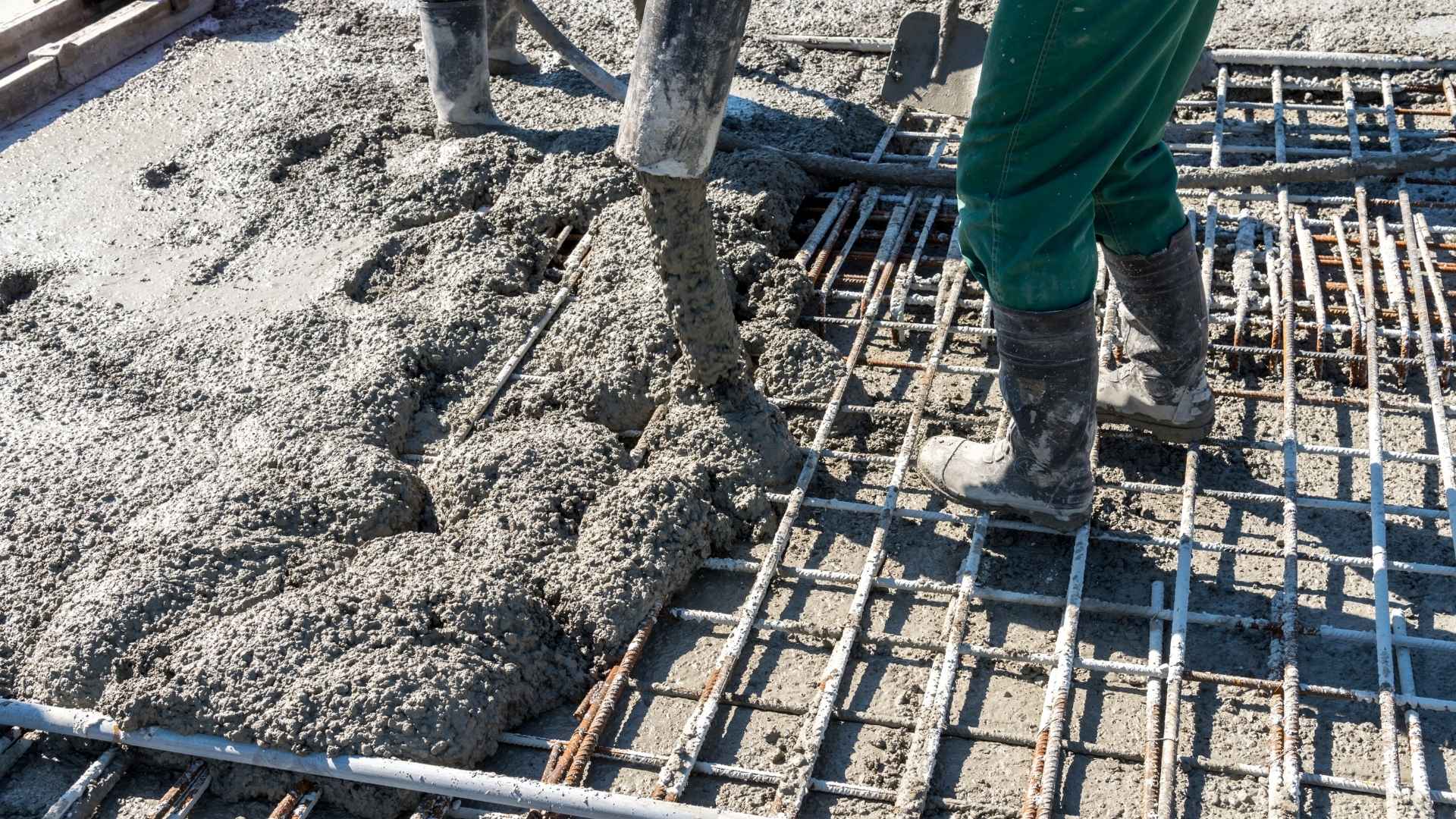
Understanding Quality Assurance (QA) Programme in Construction
Quality Assurance (QA) programmes are critical in the construction industry, ensuring that projects meet safety standards, client expectations, and regulatory requirements. A robust QA programme not only enhances the quality of the construction work but also improves overall project efficiency and client satisfaction.
What is a Quality Assurance Programme?
A Quality Assurance Programme is a systematic approach to preventing defects and ensuring that construction processes and outputs meet specified requirements. It typically includes:
- Quality Control Plans (QCP): Outlining procedures for monitoring quality throughout the project lifecycle.
- Inspection and Test Plans (ITP): Defining how materials and workmanship will be evaluated.
- Document Management System (DMS): Ensuring all quality-related documents are properly maintained and accessible.
- Non-Conformance Reporting (NCR): Tracking deviations from quality standards and implementing corrective actions.
Key Components of an Effective Quality Assurance Programme in Construction
An effective Quality Assurance Programme serves as the backbone of project success, ensuring that every construction phase — from planning to execution — meets rigorous standards of excellence and compliance.
1. Quality Management Plan (QMP)
A comprehensive Quality Management Plan serves as the foundation for all QA activities. It outlines quality objectives, roles, responsibilities, and processes to ensure compliance with standards. A construction firm may develop a QMP that specifies adherence to ISO 9001 Quality Management System standards, which helps in maintaining consistent quality across projects. This certification has been shown to enhance operational efficiency and customer satisfaction.
2. Documented Standards and Specifications
All quality standards and specifications relevant to the project must be documented. This could include international standards like ISO 9000 Quality Management System. For example, a project might reference specific ISO 9001 standards for materials used in construction to ensure compliance and quality.
3. Qualified Personnel
The QA programme should specify the qualifications required for employees, subcontractors, and suppliers involved in the construction project. For instance, a construction firm may require all welders to have relevant certification to ensure high-quality welding practices.
4. Quality Control Procedures
Detailed procedures for quality control must be established to detect issues early. This includes regular inspections, performance tests, and audits. Implementing a Quality Control Plan (QCP) outlines inspection schedules for different phases of construction, such as concrete pouring or structural framing.
5. Inspection and Test Plans
An effective QA programme must include an Inspection and Test Plan (ITP) that specifies when and how inspections will occur. For example, an ITP might detail that concrete strength tests are conducted at specified intervals during curing to ensure compliance with design specifications.
6. Non-Conformance Management
Procedures for managing non-conformances should be clearly defined. This includes documenting defects, investigating root causes, and implementing corrective actions. A construction company might use a non-conformance tracking system to log issues and monitor their resolution.
7. Training and Certification
Continuous training programs should be part of the QA strategy to ensure that all personnel are updated on best practices and regulatory requirements. For instance, holding regular workshops on Six Sigma principles, enhancing team understanding of waste reduction techniques that contribute to overall project quality.
8. Risk Assessment and Mitigation
Identifying potential risks related to quality is crucial for proactive management. A risk assessment might reveal that certain materials have a higher failure rate; thus, alternative suppliers or materials could be considered to mitigate this risk.
9. Continuous Improvement
A commitment to continuous improvement is vital for long-term success. This can involve regular reviews of QA processes and soliciting feedback from stakeholders to identify areas for enhancement. For example, using Six Sigma principles can help streamline processes and reduce waste while maintaining quality.
10. Automated Reporting Systems
Utilising technology for automated reporting can significantly enhance efficiency in tracking quality metrics. Construction quality management software can generate real-time reports on inspections, defects, and compliance checks, allowing stakeholders to make informed decisions quickly.
Steps to Implement a Quality Assurance Programme
- Define Objectives: Establish clear goals for what the QA programme should achieve.
- Appoint a Quality Manager: Designate an individual responsible for overseeing quality assurance activities throughout the project lifecycle.
- Develop a QAQC Plan: This document should outline roles, responsibilities, deliverables, communication plans, and metrics for success.
- Conduct Regular Quality Inspections: Implement a schedule for ongoing quality inspections during construction to identify potential issues early on.
- Utilise Technology: Adopt software solutions that facilitate real-time tracking of quality metrics, inspections, and documentation.
- Foster Continuous Improvement: Encourage feedback from all stakeholders to refine processes over time.
- Training & Certification: Ensure that all team members are adequately trained in quality assurance practices relevant to their roles.
Quality Assurance Best Practices in Construction
By implementing effective QA practices, construction companies can minimise defects, reduce costs, and enhance overall project outcomes. Below are some of the best practices for quality assurance in the construction industry.
1. Comprehensive Planning
Detail-Oriented Approach: Develop a detailed QA plan that outlines specific quality goals, standards, and performance metrics tailored to the project’s unique requirements. This includes identifying critical milestones where QA processes will be implemented. A construction company may set milestones for material delivery and installation phases, ensuring that quality checks are performed at each stage to prevent issues later on.
2. Regular Quality Inspections and Audits
Systematic Assessments: Conduct regular quality inspections and audits throughout the project lifecycle to assess adherence to quality standards. This proactive approach helps identify deviations early, allowing for timely corrective actions. Implementing a schedule of weekly site inspections using a standardised checklist can help identify potential quality issues before they escalate into costly problems.
3. Utilisation of Technology
Digital Integration: Leverage construction management software and technology tools to integrate QA processes into project workflows. Tools like Building Information Modelling (BIM) can provide real-time insights and facilitate better communication among stakeholders. Using drones for site inspections can enhance the accuracy of assessments, ensuring that all aspects of the construction meet predefined quality standards.
4. Continuous Improvement
Cultural Integration: Foster a culture of continuous improvement by regularly reviewing QA processes and seeking feedback from stakeholders. This approach encourages learning from past experiences and implementing lessons learned in future projects. After completing a project, conduct a debriefing session with all team members to discuss what worked well and what could be improved, documenting these insights for future reference.
5. Supplier and Material Quality Control
Holistic Approach: Extend QA practices to include rigorous control of materials and supplier processes. Collaborate closely with suppliers to establish clear expectations regarding material quality. A contractor might require suppliers to provide certification for materials used, ensuring they meet industry standards before delivery to the site.
6. Clear Definitions of Quality
Unified Understanding: Ensure that all project participants have a clear understanding of what constitutes "quality" in the context of the project. This includes documenting specific quality criteria that subcontractors and suppliers must adhere to. If sound insulation is crucial, specify that materials must exceed the legal minimum standards, ensuring everyone involved understands these requirements upfront.
7. Training and Education
Empower Staff: Regular training sessions should be conducted to keep staff updated on QA protocols, industry standards, and new technologies that can enhance quality assurance efforts. A construction firm might implement quarterly training workshops focusing on new materials or technologies that improve construction quality, ensuring all staff are proficient in current best practices.
8. Documentation and Tracking
Maintain Records: Document all quality control activities meticulously, including inspections, tests, and any identified issues along with their resolutions. This provides an audit trail that can be invaluable for compliance and continuous improvement. Using digital integrated quality management software to track QA activities allows for easy access to historical data, helping teams identify trends in recurring issues across projects.
9. Effective Communication
Continuous Interaction: Establish open lines of communication among all project stakeholders to discuss issues as they arise and verify progress against quality standards. Daily briefings can be held on-site where team members share updates on their tasks and any challenges faced, fostering a collaborative environment focused on maintaining high-quality standards.
10. Final Audits and Feedback Collection
Post-Construction Review: Conduct final audits upon project completion to ensure compliance with all specifications. Collect feedback from stakeholders to evaluate the effectiveness of the QA process. After handing over a completed building, getting feedback from clients about their satisfaction with quality can provide insights into areas for future improvement.
Digital Quality Management System
Implementing an effective Quality Assurance Programme is essential for any construction company aiming to deliver high-quality projects consistently. By integrating proven methodologies like ISO 9001 Quality Management System, Six Sigma and Total Quality Management (TQM) into your QA processes, you can significantly enhance your operational efficiency and client satisfaction levels.
If you're looking for quality software to help with your QA programme, look no further than Hubble. Contact us today to learn more about our integrated quality management system or book a demo.
Share this article
Explore Related Content
Stay up to date with our latest news features!
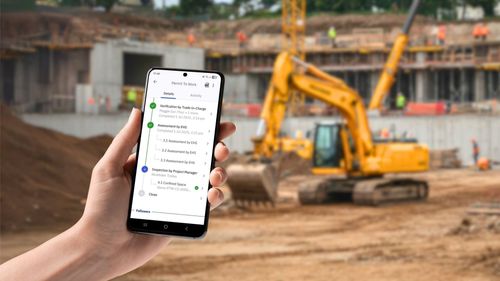
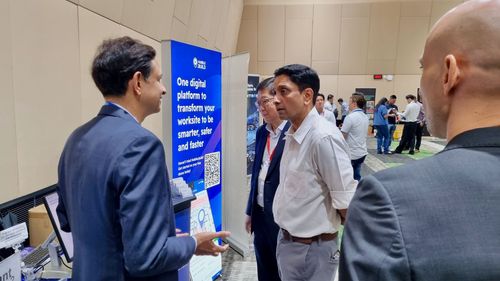
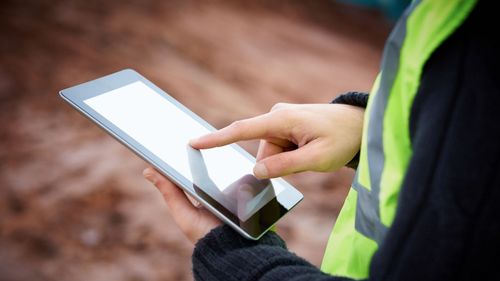