Quality inspection encompasses a systematic approach to evaluating and documenting every facet of construction — from quality of materials and workmanship to compliance with stringent standards. As we delve deeper into the role of quality inspection in construction management, it becomes clear that prioritising this function is essential for achieving long-term success in a competitive construction industry.
What is Quality Inspection in Construction
Quality inspection in construction refers to the systematic process of evaluating, measuring, and documenting the quality of materials, workmanship, and overall project execution against predetermined standards and specifications. This serves as the guardian of construction integrity, ensuring that every aspect of a project meets or exceeds the stringent requirements set forth by regulatory bodies, clients, and internal quality benchmarks.
The quality inspection acts as a safeguard against potential defects, safety hazards, and costly rework, ultimately contributing to the timely and cost-effective delivery of projects. A robust quality inspection program significantly impacts a company's reputation, customer satisfaction, and long-term profitability.
Understanding and leveraging quality inspection as a strategic asset is important. It ensures compliance with construction standards, and also positions your company as a leader in delivering quality excellence.
Understanding Quality Inspection in Singapore Context
Singapore's construction industry is renowned for its commitment to quality, and this is largely due to the implementation of comprehensive quality assessment systems.
Construction Quality Assessment System (CONQUAS)
At the forefront of these initiatives is the Construction Quality Assessment System (CONQUAS), introduced by the Building and Construction Authority (BCA) in 1989. CONQUAS serves as the national standard for assessing the construction workmanship quality of building projects, covering structural works, architectural finishes, and mechanical and electrical (M&E) systems. High CONQUAS scores have become a mark of excellence, reflecting a company's dedication to delivering superior construction outcomes.
The CONQUAS framework has evolved over time to keep pace with technological advancements and increasing quality demands. It now includes a construction quality banding system that ranks developers and builders based on their track record in private residential projects over the past six years, as well as any other validated feedback on major defects from homeowners. Introduced on 25 May 2023, this new CONQUAS banding system provides homebuyers and stakeholders with valuable insights into the expected quality of projects. Before making a property purchase, potential homebuyers can find out the bandings of developers, builders and private residential projects at the Quality Housing Portal (QHP), and make a more informed decision when buying a home.
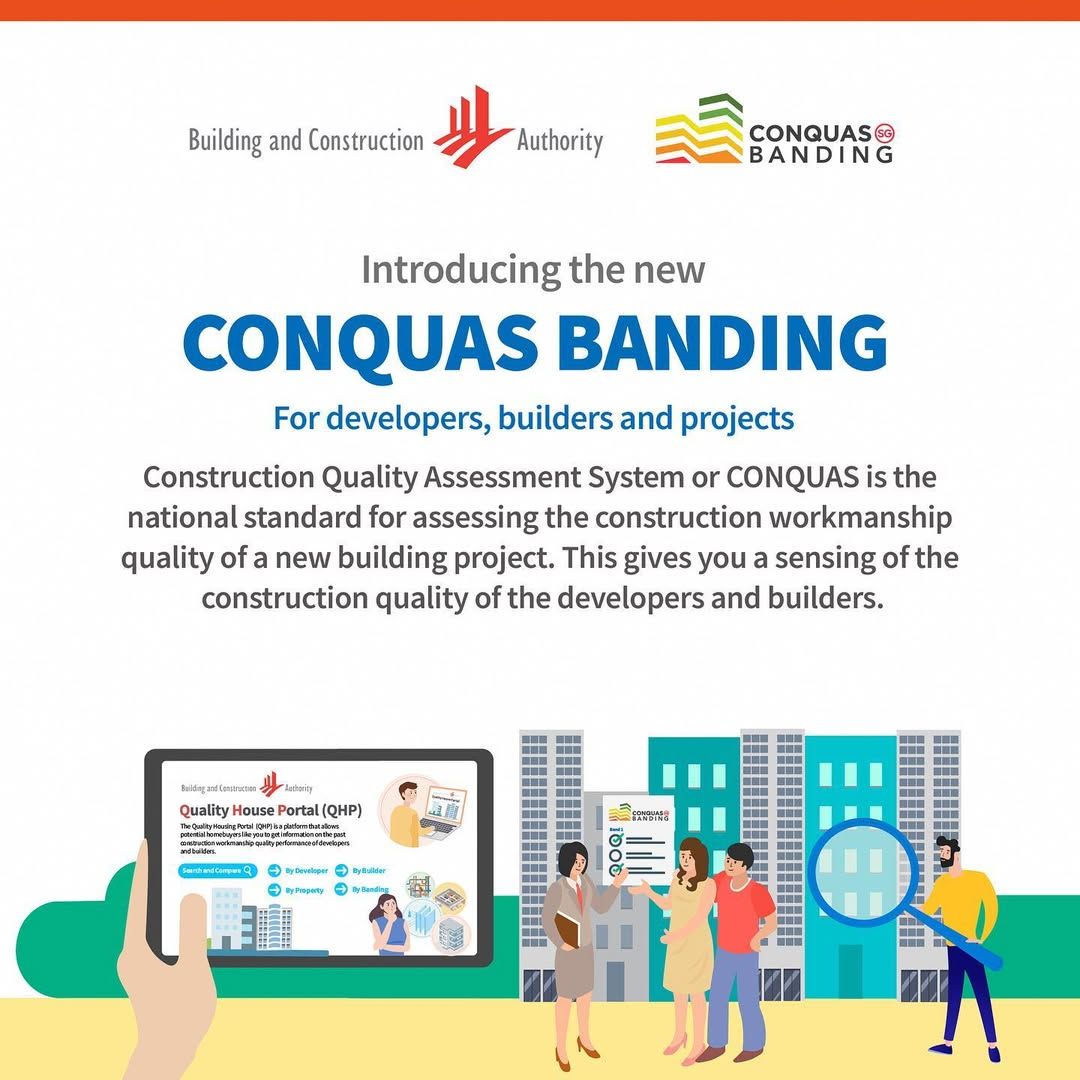
Quality Mark (QM) for Good Workmanship Certification Scheme
Complementing CONQUAS is the BCA Quality Mark (QM) for Good Workmanship Certification Scheme, specifically designed for private residential projects. This initiative, launched on 1 July 2002, aims to raise the bar for workmanship quality in homes, focusing on internal finishes and ensuring that homeowners receive properties that meet high standards of excellence.
These systems represent Singapore's commitment to maintaining its position as a global leader in construction quality. For construction companies operating in this market, aligning with and excelling in these quality assessment frameworks is crucial for success and differentiation.
Understanding Quality Inspection in Malaysia Context
Quality Assessment System in Construction (QLASSIC)
While Singapore has CONQUAS, Malaysia has implemented its own quality assessment system known as QLASSIC (Quality Assessment System in Construction). Developed by the Construction Industry Development Board (CIDB) Malaysia in 2006, QLASSIC is a scoring system and method to measure and evaluate the quality of workmanship of a construction project based on the Construction Industry Standard (CIS 7:2006). The first revision of CIS 7 was done in 2014 and the second revision was made in 2021 (CIS 7:2021). Key aspects of QLASSIC include:
- Objective Assessment: QLASSIC provides an independent method to measure the quality of workmanship in construction projects.
- Comprehensive Evaluation: It covers structural works, architectural works, mechanical and electrical (M&E) works, and external works.
- Scoring System: Projects are given a score that reflects the overall quality of workmanship, with higher scores indicating better quality.
- Industry Benchmark: QLASSIC scores serve as a benchmark for the Malaysian construction industry, encouraging continuous improvement in construction quality.
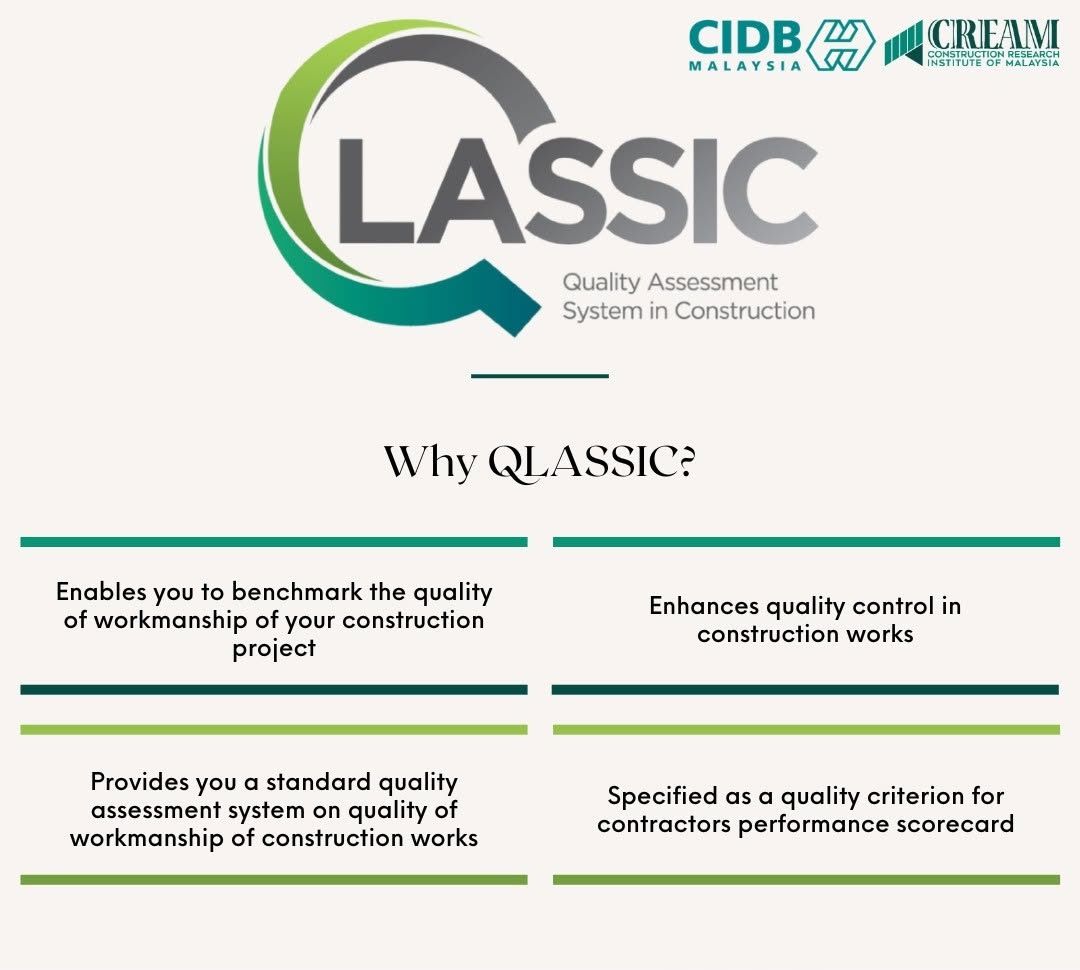
QLASSIC assessments are through site inspections conducted after the completion of a project’s building construction works, but before its handover. Construction works that are rectified after the assessment would not be reassessed for the QLASSIC score. This practice is to encourage contractors to “do things right the first time and every time”.
Read more: How QLASSIC Score Drives Construction Quality Standards in Malaysia
Benefits of Robust Quality Inspection Program
Implementing a comprehensive quality inspection program is a strategic business decision that yields significant returns. Here's why companies should prioritise quality inspection:
Cost Savings Through Early Defect Detection
Identifying and rectifying issues early in the construction process can lead to substantial cost savings. The cost of fixing a defect increases exponentially as a project progresses. A study by the Construction Industry Institute found that if an issue costs $1 to fix during the design phase, it will cost $10 during the construction phase and $100 after the construction project is completed. This exponential increase underscores the critical importance of early detection and resolution.
Implementing a comprehensive quality inspection system allows for the early identification of potential issues, leading to:
- Reduced rework costs: By catching and correcting errors before they compound, companies can significantly reduce the need for costly rework.
- Minimised material waste: Early detection prevents the unnecessary use of materials in flawed constructions, reducing waste and associated costs.
- Optimised labour efficiency: Addressing issues promptly ensures that labour resources are used efficiently, avoiding time-consuming corrections later in the project lifecycle.
Enhanced Reputation and Customer Satisfaction
In Singapore's competitive real estate market, quality is a key differentiator. Projects that consistently meet or exceed quality standards enhance a company's reputation, leading to increased customer satisfaction and positive word-of-mouth. Studies show that properties with high quality ratings command premium prices and enjoy faster sales rates. A survey commissioned by the BCA revealed that developments with CONQUAS scores above 90 experienced a 5-7% increase in property values compared to similar properties with lower scores. A research study titled "The impact of construction quality on house prices" found that well-constructed apartments not only command a higher premium price for developers, they also generate higher capital gains for homeowners and investors in the long-term. A track record of high-quality projects also improves a company's chances of winning government and private sector tenders.
Risk Mitigation and Liability Reduction
Thorough quality inspections help identify potential safety hazards and structural issues before they become critical problems. This proactive approach ensures the safety of workers and future occupants, and also significantly reduces the risk of legal liabilities and insurance claims. Implementing comprehensive quality inspection processes helps in:
- Identifying potential issues before they escalate: Regular inspections catch problems early, preventing them from becoming major liabilities.
- Ensuring regulatory compliance: Systematic quality checks ensure adherence to building codes and standards, reducing the risk of regulatory issues.
- Creating a documented trail of quality assurance: Detailed inspection records provide valuable evidence in case of disputes or claims.
Key Components of an Effective Quality Inspection Program
To harness the full potential of quality inspection, construction companies must implement a comprehensive program that encompasses all phases of a project. Here are the essential components:
1. Integration from Project Inception
Quality inspection should not be an afterthought but an integral part of the entire construction lifecycle from its very beginning. This involves:
- Involvement in design, material selection, and procurement: Quality considerations should influence decisions made during the planning and design phases, ensuring that quality is built into the project from the ground up.
- Alignment with project goals and specifications: Quality inspection criteria should be tailored to meet specific project requirements and client expectations.
2. Comprehensive Quality Inspection Types
A robust quality inspection program includes various types of inspections throughout the project lifecycle:
- Pre-construction inspections: These assess the quality of materials and ensure proper site preparation.
- In-progress inspections: Regular checks during construction help identify and correct issues promptly.
- Final inspections: Comprehensive evaluations ensure that the completed work meets all quality standards before handover.
- Specialised inspections: For complex systems like structural integrity or MEP installations, specialised inspections by experts are crucial.
3. Technology-Driven Inspection Processes
Leveraging technology can significantly enhance the efficiency and effectiveness of quality inspections:
- Digital checklists and mobile quality inspection apps: These tools facilitate photo and video documentation of issues, and streamline the inspection process, ensuring consistency.
- Real-time data collection and analysis: Immediate access to inspection data allows for quick decision-making and issue resolution.
- Integration with Document Management System: Instant access to project documents, e.g. Inspection and Test Plans (ITP), serves as a point of reference for stakeholders in the project.
4. Data-Driven Decision Making
Modern quality inspection programs should leverage data to drive continuous improvement:
- Key Performance Indicators (KPIs) for quality: Establish and track quality metrics that reflect the quality performance of projects and teams.
- Trend analysis and predictive quality management: Use historical data to identify patterns and predict potential quality issues before they occur.
- Continuous improvement strategies: Regularly review inspection data to refine processes and enhance overall quality management.
Implementing a Quality Inspection Program
Consider the following implementation strategies to elevate your company’s quality inspection capabilities:
1. Developing a Quality Control Plan (QCP)
A comprehensive quality control plan is the foundation of effective quality inspection:
- Setting clear quality standards and objectives: Define specific, measurable quality targets aligned with industry benchmarks, such as CONQUAS, and industry best practices.
- Defining roles and responsibilities: Clearly outline who is responsible for various aspects of quality inspection and management, e.g. Quality Control Manager, Project Managers, Site Supervisors, Subcontractors, Quality Inspectors.
- Establishing inspection schedules and protocols: Create a structured approach to inspections that covers all critical phases and components of construction.
2. Training and Skill Development
Investing in your workforce is crucial for maintaining high-quality standards:
- Cultivating a quality-focused workforce: Foster a culture where quality is everyone's responsibility, from site workers to top management.
- Certification programs for inspectors: Encourage professional certifications to ensure your inspection team is highly skilled and up-to-date with industry standards.
- Ongoing education on latest industry standards: Regularly update your team on changes in regulations, technologies, and best practices in quality inspection.
3. Leveraging Third-Party Quality Inspection Services
While internal quality control is essential, third-party quality inspections offer additional benefits:
- Benefits of independent quality assurance: External inspectors provide an unbiased assessment and can offer fresh perspectives on quality improvement.
- Selecting the right inspection partner: Choose reputable inspection companies with extensive experience in your specific sector of the construction industry and a track record of working with top developers.
4. Compliance and Regulatory Considerations
Staying compliant with local and international standards is critical:
- Adhering to standards and regulations: Ensure your quality inspection program aligns with local requirements. In Singapore, this includes regulations set by the BCA and other relevant government bodies.
- International quality management standards: Consider implementing ISO 9001 Quality Management System or other relevant international standards to demonstrate your commitment to quality globally.
Advanced Quality Inspection Techniques
To stay ahead in the competitive construction market, consider incorporating these advanced techniques:
1. Non-Destructive Testing (NDT) Methods
- NDT techniques relevant to construction: Familiarise your team with methods like ultrasonic testing, thermography, and ground-penetrating radar.
- Applications in structural integrity assessment: Use NDT to evaluate the strength and durability of concrete structures without causing damage.
2. Drone and AI-Powered Inspections
- Aerial inspections for large-scale projects: Utilise drones for efficient and safe inspections of hard-to-reach areas that are dangerous or time-consuming for human inspectors, such as tall structures or expansive construction sites.
- Machine learning for defect detection and analysis: Implement AI algorithms to analyse inspection data and identify patterns or anomalies that human inspectors might miss.
3. IoT and Sensor-Based Quality Monitoring
- Real-time monitoring of critical parameters: Deploy IoT sensors to continuously monitor factors like concrete curing conditions or structural loads.
- Predictive maintenance applications: Use IoT data to anticipate maintenance needs and prevent quality issues before they occur.
Overcoming Challenges in Quality Inspection
Implementing a quality inspection program is not without its challenges:
1. Managing Quality Across Multiple Subcontractors and Suppliers
In today's complex construction projects, managing quality across numerous subcontractors and suppliers presents a significant challenge. Ensuring consistent standards and seamless integration of work from various parties is crucial for project success. Some challenges in multi-party quality management includes:
- Inconsistent quality standards across different subcontractors
- Communication gaps leading to misaligned expectations
- Difficulty in tracking and enforcing compliance
- Increased risk of defects at interface points between different work packages
7 Effective Strategies for Quality Management
To overcome these challenges and maintain high-quality standards across all project participants, consider the following QUALITY approach:
Q - Quantify Standards Clearly
- Develop comprehensive quality management plans that clearly define standards, processes, and responsibilities for all parties involved.
- Ensure these standards are communicated effectively and understood by all subcontractors and suppliers.
U - Utilise Integrated Construction Management Software
- Implement a centralised platform for quality management that allows real-time monitoring, reporting, and collaboration across all project stakeholders.
- Ensure the software provides features such as:
- Digital checklists and inspection forms
- Real-time defect tracking and resolution
- Automated notifications and escalations
- Data analytics for identifying trends and areas for improvement
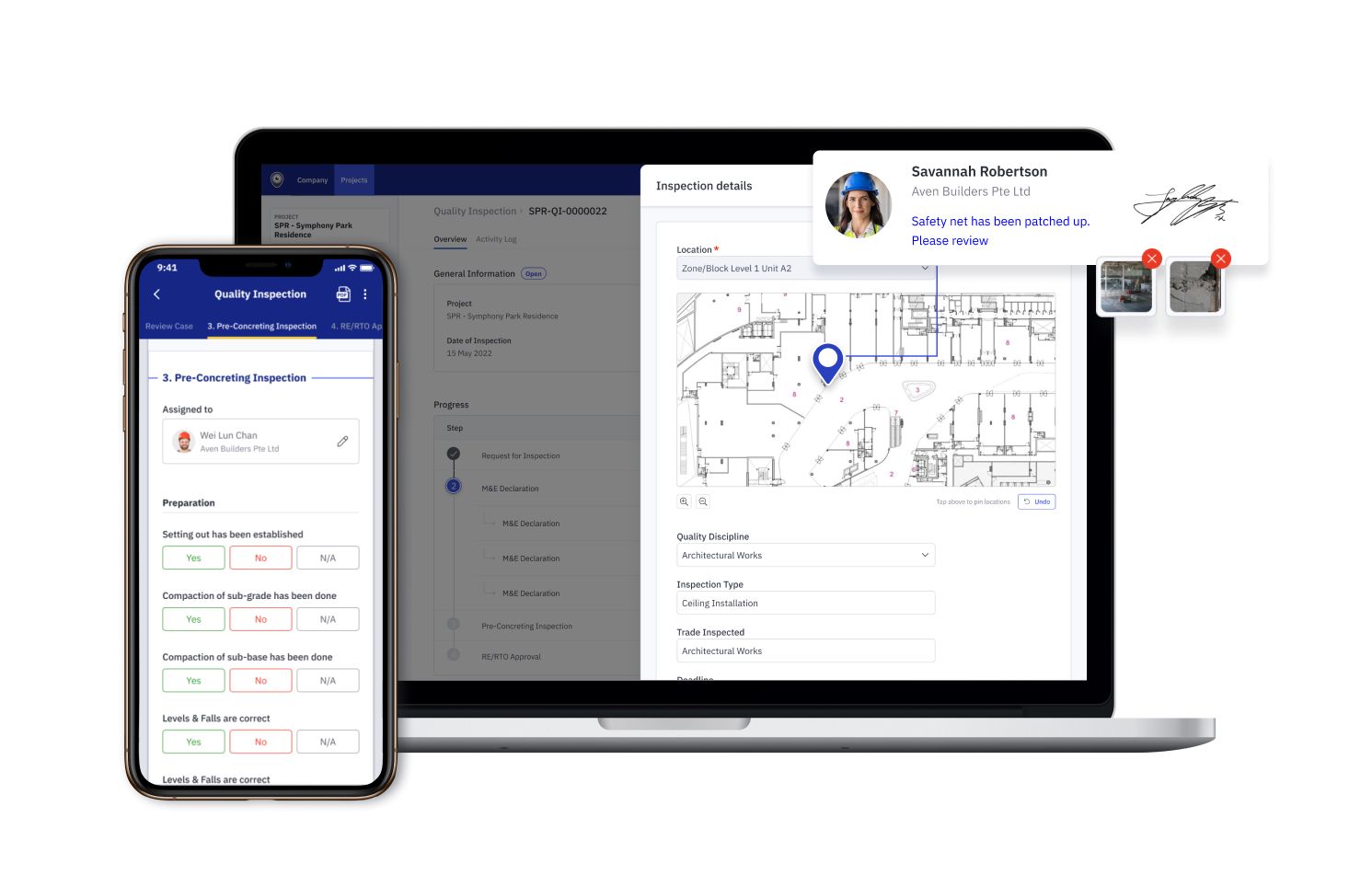
A - Audit Regularly with Inspections
- Establish a schedule of regular quality audits and inspections for all subcontractors and suppliers.
- Use a mix of announced and unannounced inspections to ensure consistent quality standards are maintained.
L - Lead by Fostering a Culture of Collaboration and Continuous Improvement
- Organise regular quality coordination meetings with all key stakeholders to discuss issues, share best practices, and align on quality objectives.
- Implement a system for collecting and acting on feedback from subcontractors and suppliers to continuously improve processes.
I - Implement a Robust Non-Conformance Management System
- Establish clear procedures for identifying, reporting, and addressing non-conformances.
- Ensure timely corrective actions and follow-ups to prevent recurrence of issues.
T - Train and Support Subcontractors
- Offer training sessions on your quality standards and processes to ensure all parties are aligned.
- Provide resources and support to help subcontractors meet your quality requirements.
Y - Yield Insights from Data Analytics for Proactive Quality Management
- Use data from inspections and audits to identify patterns and trends in quality issues.
- Implement predictive analytics to anticipate potential quality problems before they occur.
By implementing these QUALITY strategies, you can create a cohesive quality management ecosystem that spans across all subcontractors and suppliers, ensuring consistent high-quality outcomes throughout your projects.
2. Balancing Quality Requirements with Project Timelines and Budgets
Another persistent challenge in construction project management is striking the right balance between maintaining high-quality standards and meeting project timelines and budgets. This delicate equilibrium is often referred to as the "project management triangle" or the "triple constraint," where quality, time, and cost are interconnected, and changes in one aspect inevitably affect the others. Understanding the relationship between these three factors is crucial:
- Improving quality often requires more time and resources, potentially increasing costs and extending timelines.
- Accelerating timelines may lead to rushed work and compromised quality, or increased costs for additional resources.
- Reducing costs could result in the use of lower-quality materials or less experienced personnel, potentially affecting both quality and timelines.
10 Strategies for Optimising the Balance of Quality, Time, and Cost
To effectively balance quality requirements with project timelines and budgets, consider implementing the following strategies:
1. Implement Comprehensive Planning and Risk Management
- Conduct thorough project planning that includes detailed quality requirements, realistic timelines, and accurate budget estimates.
- Perform a comprehensive risk assessment to identify potential quality, time, and cost risks early in the project.
- Develop contingency plans for identified risks to minimise their impact on project outcomes.
2. Prioritise Quality Requirements
- Clearly define and prioritise quality requirements based on their criticality to project success and client satisfaction.
- Focus resources on high-priority quality aspects while identifying areas where compromises can be made if necessary.
3. Leverage Technology for Efficiency and Quality Control
- Utilise Building Information Modelling (BIM) to improve coordination, reduce errors, and enhance overall quality.
- Implement automated quality control systems and IoT sensors for real-time monitoring of critical quality parameters.
4. Enhance Communication and Collaboration
- Establish clear communication channels and protocols among all project stakeholders.
- Use collaborative project management tools to ensure all parties are aligned on quality expectations, timelines, and budgets.
5. Implement Stage-Gate Processes
- Establish quality checkpoints at critical project stages to ensure quality standards are met before proceeding to the next phase.
- This approach helps identify and address quality issues early, preventing costly rework and delays later in the project.
6. Optimise Resource Allocation
- Use resource levelling techniques to ensure efficient utilisation of personnel and equipment across the project timeline.
- Consider the use of prefabrication and modular construction techniques to improve quality control and reduce on-site timelines.
7. Implement Value Engineering
- Conduct value engineering exercises to identify opportunities for cost savings without compromising on essential quality requirements.
- Focus on lifecycle costs rather than just initial construction costs to ensure long-term quality and value.
8. Establish a Robust Change Management Process
- Implement a structured change management process to evaluate the impact of proposed changes on quality, time, and cost.
- Ensure all stakeholders understand the implications of changes before approval.
9. Continuous Monitoring and Adaptation
- Implement real-time project monitoring systems to track progress against quality, time, and cost targets.
- Use data analytics to identify trends and make informed decisions on resource allocation and prioritisation.
10. Invest in Quality Training and Culture
- Provide ongoing training to project teams on quality management techniques and best practices.
- Foster a culture of quality awareness and continuous improvement across the organisation.
By implementing these strategies, construction leaders can navigate the complex interplay between quality, time, and cost more effectively. The key lies in proactive planning, leveraging technology, fostering collaboration, and maintaining flexibility to adapt to changing project dynamics.
Elevating Construction Excellence Through Quality Inspection
Quality inspection is not merely a regulatory requirement or a cost centre; it is a strategic imperative that can drive organisational success, enhance market position, and contribute to the overall excellence of Singapore's built environment. By investing in robust quality inspection programs, leveraging advanced technologies, and fostering a culture of quality, construction and real estate development companies can position themselves as leaders in an increasingly competitive market.
Prioritising quality inspection is an investment in your company's future. It's time to elevate quality inspection from a compliance activity to a core business strategy that drives growth, reputation, and long-term success in the dynamic construction industry.
Share this article
Explore Related Content
Stay up to date with our latest news features!
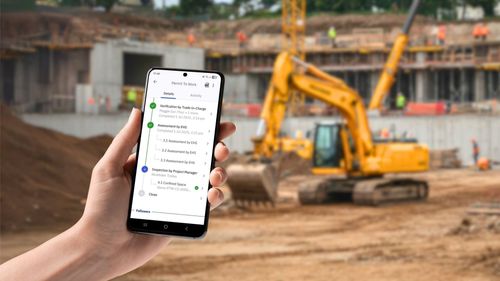
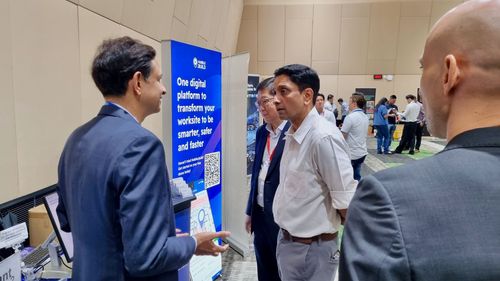
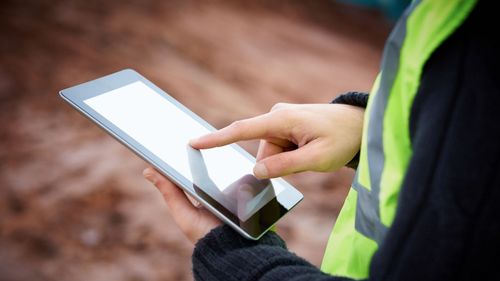