2024 in Review: Beyond Growth to Transformation
Mega-infrastructure projects like Changi Airport Terminal 5 and the Cross Island MRT Line dominate headlines in 2024, adding to the year of robust growth with projected demand between S$32 billion and S$38 billion. Yet, the real story lies in how the construction industry is transforming.
Beyond the numbers, regulatory shifts, rising expectations for quality and safety, and advancements in technology are reshaping how Singapore builds, manages, and sustains its urban environment.
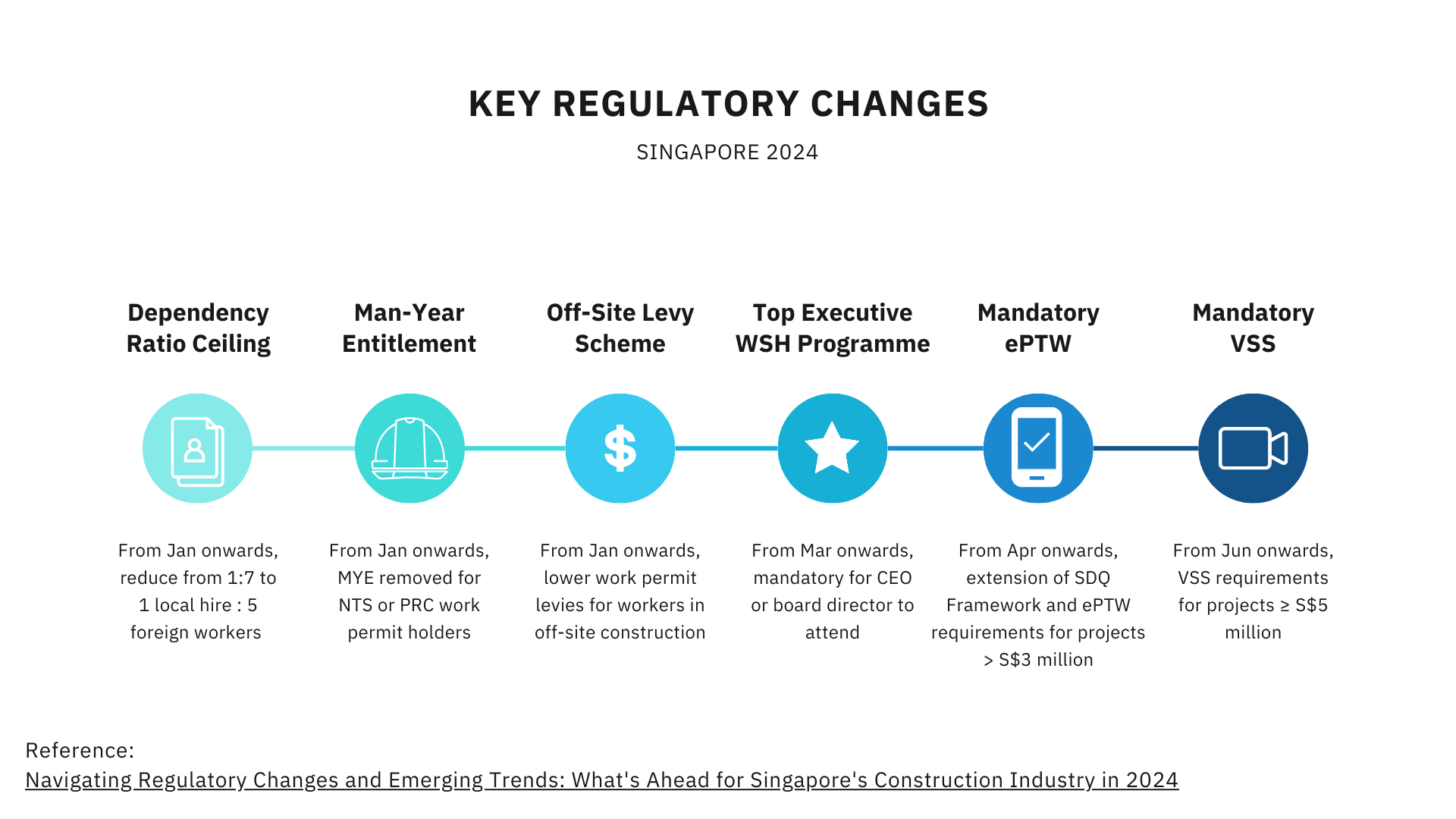
These changes underline Singapore’s commitment to modernising the industry, enhancing safety, and fostering a more sustainable and productive construction environment.
Key Trends Shaping the Industry
From Quantity to Quality

Singapore’s construction industry is transitioning from a focus on sheer scale to delivering higher-quality, sustainable, and safer projects. This shift reflects heightened expectations from clients, regulators, and the broader community.
- Rising Standards: The Contractors Registration System (CRS) now sets higher benchmarks for financial capability, operational experience, and a solid track record. This emphasises quality as a non-negotiable element for earning trust and securing projects.
- Safety as a Core Metric: Initiatives like the Safety Disqualification (SDQ) Framework as well as mandatory use of electronic Permit-to-Work (ePTW) systems and Video Surveillance Systems (VSS) elevate safety from compliance to a critical quality benchmark. Proactive safety management, such as IoT-enabled real-time resource tracking, AI-based video analytics for 24/7 site monitoring, and leadership-led safety culture is becoming a key differentiator and a competitive advantage for firms, especially in high-value projects.
- Sustainability’s Role in Quality: Green certifications, energy-efficient materials, and sustainable practices are increasingly necessary, reflecting global priorities for environmentally responsible development.
Firms that embed quality and safety into their operations position themselves to meet regulatory expectations and build long-term credibility. Integrated systems, like those offered by Hubble, can facilitate this shift by enabling real-time monitoring, automated checks, and streamlined data-driven processes across all stages of a project.
Labour and Cost Pressures Highlight Productivity Gaps
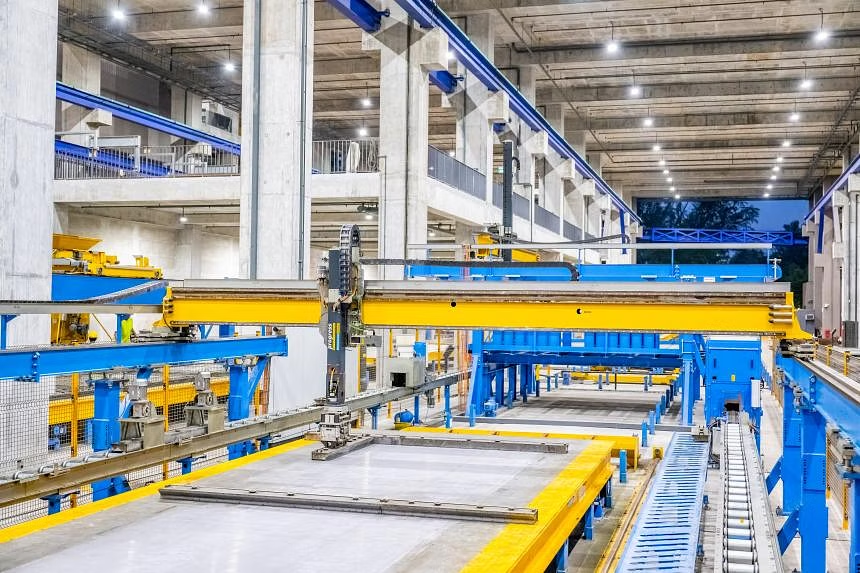
Rising material costs and tightening labour quotas continue to expose inefficiencies in traditional methods, pushing firms to rethink how they approach construction processes and innovate.
- Adoption of Modular Construction: Prefabrication techniques like Design for Manufacturing and Assembly (DfMA) and Integrated Digital Delivery (IDD) improve build times, reduce manpower needs, and offer scalability, ensuring predictability in both costs and timelines.
- Policy Incentives: Schemes like the Off-Site Levy Scheme (OLS) and Productivity Innovation Project (PIP) incentivise firms to invest in off-site production and automation, easing labour constraints while maintaining build quality.
- Workforce Development: Upskilling programs are essential to complement automation, ensuring human expertise aligns with technological advancements.
Addressing productivity gaps requires a combination of rethinking workflows and leveraging technology to ensure precision and coordination. Platforms like Fabrication Management System play a pivotal role by synchronising off-site production with on-site assembly, helping firms deliver with accuracy and efficiency.
Unlocking the Power of Data
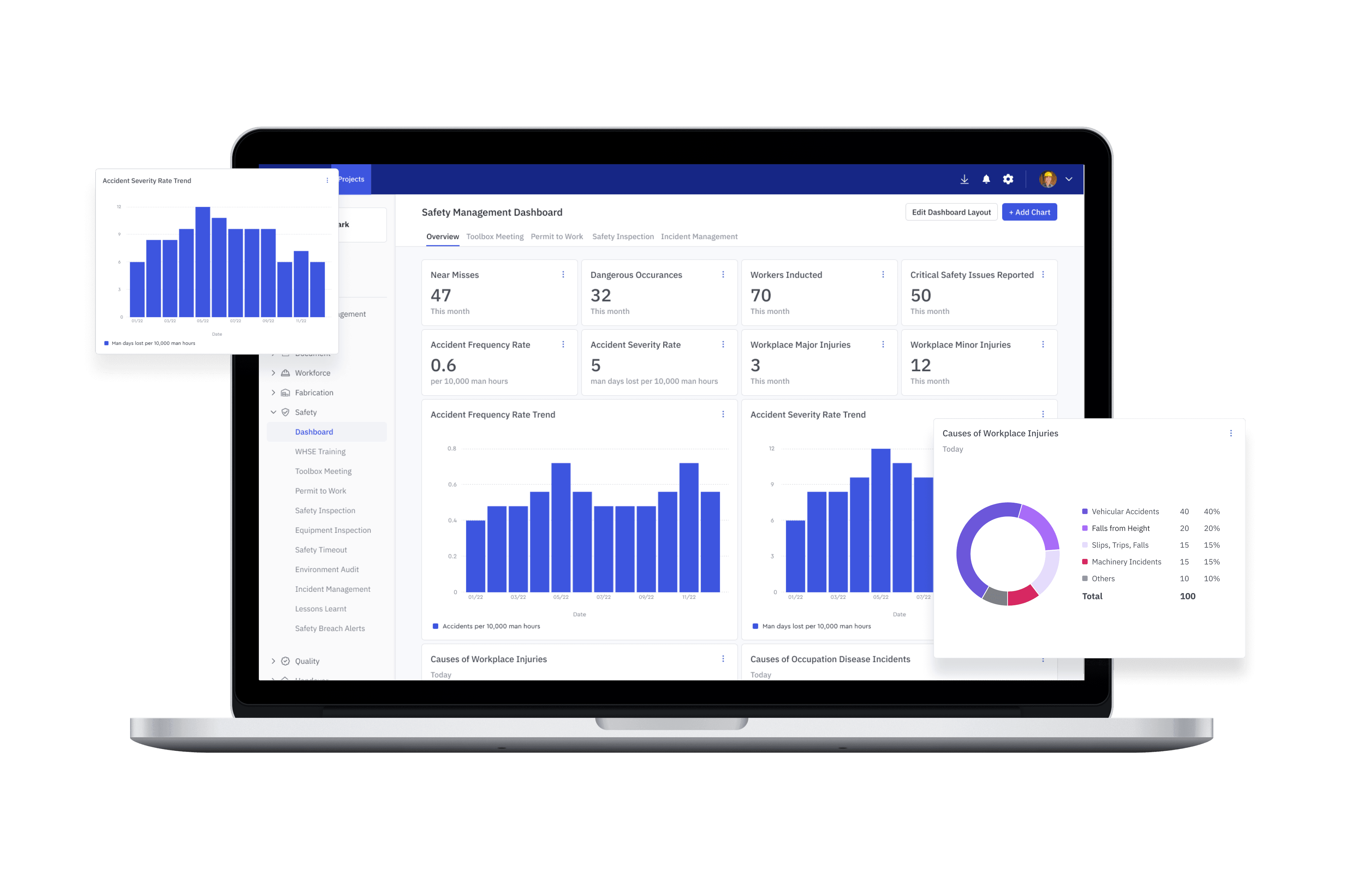
Construction generates vast amounts of data—from site activities to supply chain metrics—but much of it still remains siloed and underutilised. This often leads to inefficiencies in decision-making and execution, from workforce management to safety compliance, and progress tracking. Firms that effectively harness this data can unlock significant operational advantages.
- Breaking Down Silos: Integrated systems that consolidate safety, quality, and workforce data provide a single source of truth, enabling real-time, data-driven decision-making.
- Workforce Optimisation: With tighter quotas on foreign workers, tools like ePSS reports provide actionable insights into labour allocation and productivity, helping firms identify areas for optimisation, including reallocating skilled workers or automating repetitive tasks.
- Anticipating Risks: Predictive analytics and centralised platforms empower firms to foresee potential delays, mitigate risks, and maintain alignment across stakeholders.
Data integration, while technologically challenging, is a strategic priority with real-time visibility that can transform project outcomes, from resource allocation to risk management. Hubble’s integrated platform centralises data streams, enabling firms to move from reactive response to proactive, data-driven strategies.
Opportunities for 2025 and Beyond: Building Smarter for the Future
As Singapore’s construction industry moves into 2025, its accelerating growth and transformation will be driven by a commitment to quality, an urgency to close productivity gaps, and the power of data. Firms that embrace these shifts will not only adapt but thrive, setting new standards for the built environment.
The integration of smart technological solutions will be integral for this critical time, from real-time visibility to multi-stakeholder coordination and accurate progress oversight.
And it isn’t just about adopting tools—it’s about rethinking how projects are planned, executed, and delivered. Discover how Hubble’s solutions can support your team in shaping the future of construction.
Share this article
Explore Related Content
Stay up to date with our latest news features!
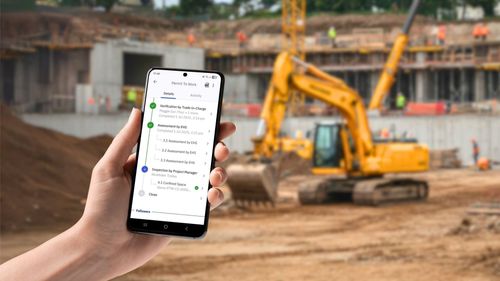
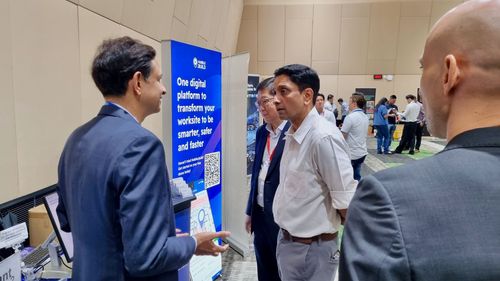
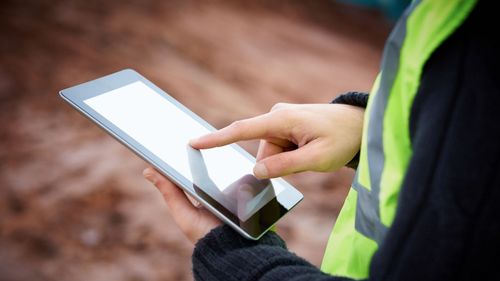